Purpose
- Scientific and technological assistance of launchers and spacecraft development
- Theoretical and experimental research of processes in rocket and space objects elements
- Development of software for research and design work
- Development and investigations of samples of rocket and space objects components
- Scientific and technological assistance of requirement specifications, projects, production and operation for rocket and space objects.
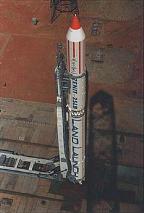
Services
- Mathematical modeling of liquefied launchers longitudinal vibrations with taking into account cavitational phenomena in liquid propellant rocket engine pumps
- Mathematical modeling of liquid propellant rocket engines injectionInvestigation of “liquid propellant rocket engine launcher airframe” system dynamic stability
- Development of mainly new means to ensure liquefied launchers longitudinal stability
- Analysis of dynamic compatibility of the liquid propellant rocket engine with the launcher design
- Prediction of dynamic response (longitudinal accelerations) of spacecraft during injection and flight of the liquefied launcher
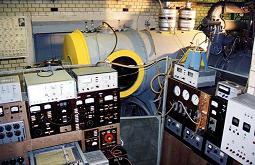
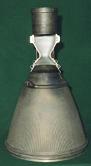
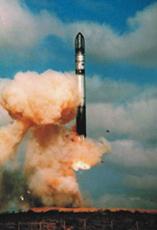
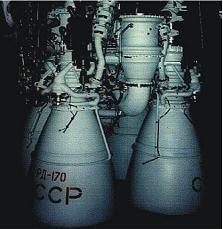
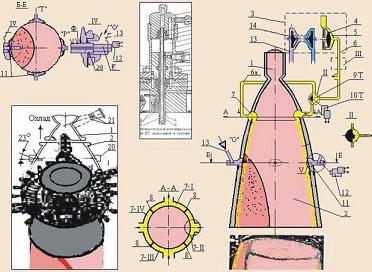
- Use of plasma electrodynamic facility to simulate operational conditions, motion and flow regimes, spacecraft and Solar system planets interaction with interplanetary medium (solar wind), cold and hot plasma, charged particles flows, electric and magnetic fields, solar spectrum and radar waveband electric and magnetic radiation in the Earth ionosphere and magnetosphere at elliptical, geostationary and geopolar orbits at heights of 150 – 40000 km
- Vacuum-arch techniques for plasma condensate coating high-heat surfaces of liquid propellant rocket engine combustion chambers
- Heat-resistant coatings for liquid propellant rocket engine combustion chambers; corrosion-resistant and barrier coatings for composite materials units (copper-carbon, copper-tungsten)
- Dynamic design of highly maneuverable controlled objects with a simultaneous selection of their basic design and operating parameters
- Determination of characteristics of spacecraft gas-liquid systems, operating in conditions of weightlessness and alternating loading
- Calculation of motion parameters and optimization of rocket motion control software
- Hydrogasdynamics and unsteady heat-and-mass transfer in jet engines
- Supersonic and subsonic gas flow control
- Gasdynamic control of rocket engine thrust vector
- Development of bifunctional system of thrust vector control of a space rocket stage main engine with a large mass asymmetry
- Evaluation of dynamic response of rocket-space technology elements at various kinds of starting
- Evaluation of characteristics of spacecraft opening process and elements stress-strain-state
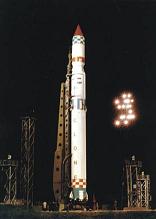
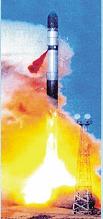
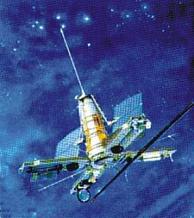
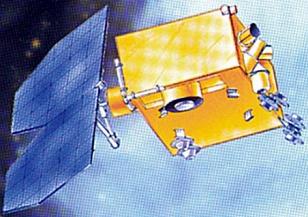
- Strength and carrying capacity of shell-and-rod structure of scpacecraft under extremal conditions
- Reliability and durability of space and rocket technology products
- Models of damage accumulation
- Load regimes equivalent to operational ones
- Engineering diagnostics of the state of the structure elements based on application of the physical phenomena within materials
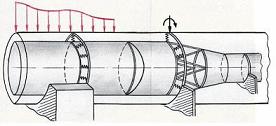
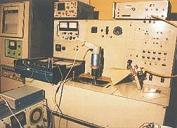
- Evaluation of residual life
- Development of improvements in the functional properties of structural materials
- Aerogasdynamics of rocket and space technology objects, computational aero-thermogasdynamics of launch vehicles, re-entry spacecraft, passages of hypersonic ramjet engines and control jet thrusters
- Theoretical and experimental studies on jet flows, launch vehicles start gasdynamics and thermostatic parameters of launch vehicles sections and technological devices
- Calculations of supersonic flows around launch vehicles
- Determination of parameters of controlling two component liquid propellant rocket engine of small thrust
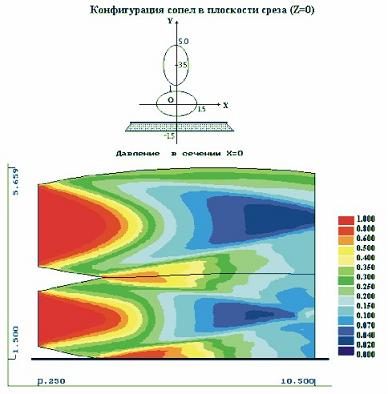
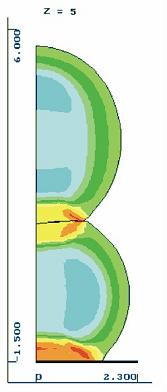
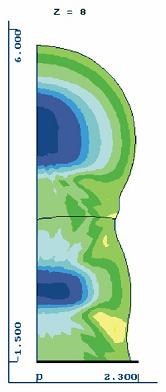
- Study of spacecraft vibration loading at transportation
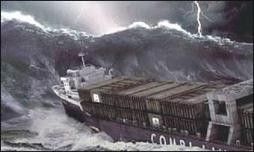

- Determination of parameters of launch vehicles trajectories and spacecraft orbits by measuring data of navigation satellites and earth stations
- Space and rocket objects control
- Systems analysis of space activities
- Optimization of superlight space rocket design parameters and motion control software
- Space debris population dynamics analysis. Theoretical and experimental studies of means for the prevention of near-Earth space pollution from operating and used launch vehicles and spacecraft
- Analysis of perspective space systems
- Simulation of space cable system motion
- Methods to study dynamics of perspective spacecraft
- Study of aerodynamic, thermal, photometric characteristics and processes of mass transfer in the region of orbital and re-entry spacecraft
- Laboratory flight simulation, experimental investigations of features of the rarefied gas supersonic neutral flow/streamlined surface interaction
- Сoncepts development, formulation and realization of space scientific and applied experiments
- Experimental studies and aerogasdynamic maintenance of space projects
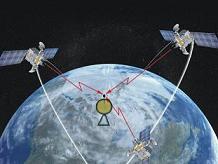
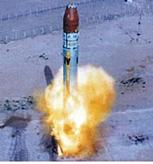
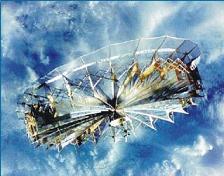
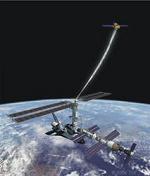
Expert examination
- Preparation of a performance/requirements specification (requirements specification ) for space equipment object development
- Design (pilot project, draft design, detail design) examination
- Space equipment object experimental development package plan examination
- Consideration of the results of work on the space equipment object development and manufacturing
- Space equipment object flight test preparedness substantiation
- Analysis of the subcontractors’ normative documents employed in the space equipment object components development and manufacturing
Preparation of expert’s conclusions on space equipment object designs includes
- Performance/requirements specification (requirements specification) compliance analysis
- Comparative analysis of the proposed engineering solutions and basic performance characteristics of the space equipment object under development as against its best domestic and foreign counterparts
- Assessment of the expected space equipment object efficiency
- Assessment of the space equipment object competitive ability in the world market of space services
- Normative requirements compliance assessment
- Preparation of recommendations on the introduction of the obtained achievements into other industries
Contact information: | |
Institute of Technical Mechanics of the NASU and SSAU | |
Ukraine 49005 Dnipro 15 Leshko-Popel St. | |
Contact person: | O. V. Pylypenko |
Phone: | (056) 372 06 50 |
E-mail: | OPylypenko@nas.gov.ua |
Web: | http://www.itm.dp.ua |