Head of department – D.Sc., Senior Researcher Yuri O. Kvasha
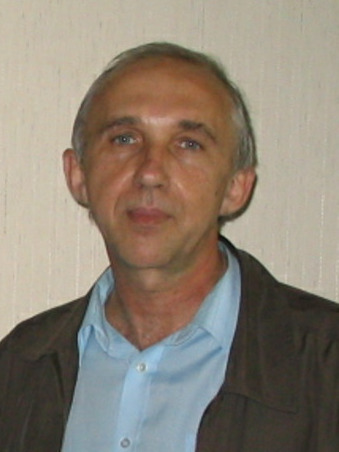
Field of research – liquid-propellant rocket propulsion systems dynamics; liquid-propellant launch vehicle pogo stability; development of radically new dampers to provide the pogo stability of liquid-propellant rockets; vibration protection systems dynamics; heat exchange of blade machines; dynamics of hydraulic systems with cavitating elements; development of the fundamentals of the theory and design of report reduction device – small-arms silencer.
Liquid-propellant rocket propulsion systems dynamics
Under certain conditions, cavitation in screw centrifugal pumps of liquid propellant rocket propulsion systems (LPRPSs) can cause self-excited low-frequency (from 4 to 50 Hz) self-oscillations of pressure and flow rate of fuel components in the power feed systems of the LRE. Cavitation self-oscillations interfere, and sometimes make impossible the normal functioning of the pump power feed system of rocket propulsion systems during rocket flight. Some aspects of the problem of cavitation self-oscillations were considered both in the former USSR and abroad (USA, Japan, France, etc.). The employees of the Department of Dynamics of Hydromechanical and Vibration Protection Systems made a decisive contribution to solving the problem of cavitation self-oscillations. The results of systematic theoretical and experimental studies of low-frequency cavitation self-oscillations in the pump power feed systems of liquid propellant rocket engines, performed by the department, made it possible to form new ideas about the dynamic processes in such installations. The theory of low-frequency cavitation self-oscillations in pump power feed systems for liquid propellant rocket engines was created, which makes it possible to predict the stability of the pump power feed system for liquid propellant rocket engines with respect to cavitation oscillations (and in the case of loss of stability of the pump system, to predict the amplitudes, frequencies and waveforms) and conduct a quantitative analysis of the influence of structural and operating parameters of the system for cavitation self-oscillations. Its probability is confirmed by the satisfactory convergence of the calculated and experimental frequencies of cavitation oscillations, the boundaries of the stability regions in the plane of various operating parameters of the pump system (for example, the liquid pressure at the pump inlet – the liquid flow through the pump), the dynamic characteristics of screw centrifugal pumps and liquid propellant feed systems, and the parameters of cavitation self-oscillations in the pumping system. In this regard, it is used to solve a wide range of problems in the dynamics of liquid propellant rocket engines and a theoretical study of the POGO stability of liquid launch vehicles (LV).
Based on this theory, effective methods and means have been developed for eliminating cavitation self-oscillations in pump power feed systems of liquid propellant rocket engines, which are implemented in the Yuzhnoye State Design Office and Energomash Research and Production Association (Russia).
The cavitation self-oscillation theory made it possible to approach the linear and nonlinear dynamics of LPRE and rocket dynamics as a whole (determining the frequency characteristics and calculating the process of starting liquid-propellant rocket engines (LRE), analyzing the POGO stability of the launch vehicle and estimating the amplitudes of the rocket body POGO vibrations).
In 1995, under the contract of ITM NASU and SSAU with the European Rocket Engine Development and Production Amalgamation (SEP), theoretical studies of cavitation self-oscillations in the VULCAIN liquid oxygen fuel feed system (which was developed for the ARIAN-5 launch vehicle) were carried out, which arose during its offline tests. From a theoretical point of view, the experimentally determined loss of stability of the specified power system was explained and the effectiveness of measures aimed at eliminating cavitation self-oscillations was substantiated.
The problem issues of LPRPS dynamics involving mathematical simulation of the engine starting process and LPRPS transients in emergencies have been resolved.
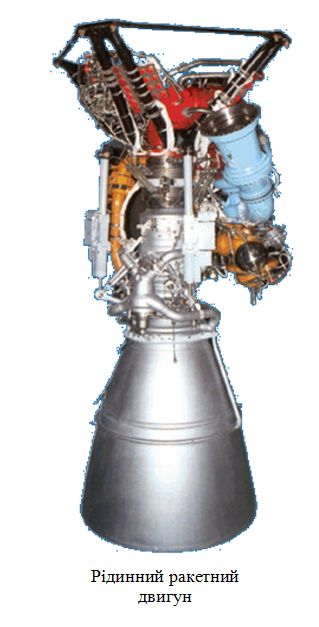
The requirements have been formulated to approximate bench conditions for launch vehicle engine tests to full-scale tests in terms of hydrodynamics of feed lines.
Mathematical simulation of the joint POGO and POGO-bending vibrations of the design of the feed pipelines and fluid in hydraulic systems with LPRE cavitation pumps. Linear and nonlinear mathematical models of joint POGO vibrations of the construction of a rectilinear pipeline and fluid have been developed. The developed mathematical models allow us to study the stability of hydraulic systems with LPRE cavitation pumps with respect to cavitation oscillations and determine the parameters of cavitation self-oscillations.
A numerical study of the stability of low-frequency processes in a rocket engine and determining the causes of oscillations in the engine is an integral part of the work in the development of a rocket engine. The possibility of implementing various mechanisms for the loss of stability of the working process in an engine requires the development of a sufficiently detailed mathematical model of the low-frequency dynamics of the engine. When modeling low-frequency processes in a liquid-propellant rocket engine with generator gas afterburning, it is necessary to take into account cavitation phenomena in pumps, feedbacks between oscillatory processes in a gas generator and pumps, non-isothermal processes in a gas generator and gas ducts, gas generation time delays, dynamic processes in a flow regulator. Based on modern ideas about the dynamics of liquid-propellant rocket engines with afterburning of the generator gas, mathematical models of dynamic processes in the elements of a promising marching rocket engine of the indicated type at launch are developed. Mathematical modeling of the launch process of the marching rocket engine is performed. It is established that taking into account delays in the mathematical model of the low-frequency dynamics of the gas generator and the gas rail engine with afterburning of the generator gas significantly affects the transient processes in the engine when it starts. It is shown that taking into account cavitation in engine pumps significantly increases the reliability of the results of mathematical modeling of the launch process of a marching rocket engine.
A method has been developed to determine the motion parameters of the interface between the gas and liquid media in the cavities of the fuel tanks of modern space stages of liquid rockets under the conditions of microgravity (between the start and shutdown of mid-flight engines of space stages), taking into account the design features of the inner tank devices for ensuring the continuity of liquid fuel components. The developed methodology was tested with the use of experimental data obtained for a model tank in a “throw tower”. Using this development will allow, at the design stage of the marching liquid propellant rocket engine, to evaluate the efficiency of the internal tank devices to prevent the penetration of boost gas at the engine inlet in quantities that are unacceptable for starting it.
Liquid-propellant launch vehicle pogo stability
Developers of multistage liquid launch vehicles in Ukraine, Russia, the USA, France and other countries inevitably face the problem of ensuring the POGO stability of the launch vehicle. This problem requires its analysis and solution in the development of new and modernization of existing LV in each case. The need for its theoretical solution is due to the fact that the fact of stability (or loss of stability) of liquid-propellant launch vehicles cannot be determined experimentally in ground conditions, it can only be established during flight design tests of the launch vehicle. The elimination of POGO fluctuations of the pH detected during such field tests, or the reduction of the amplitudes of these oscillations to a safe level requires significant material and financial costs. To exclude such expenses, it is necessary to carry out the maximum possible volume of computational studies of the POGO stability of a specific launch vehicle at the initial stages of development or modernization of missiles based on mathematical models that most fully describe the dynamic processes in liquid-propellant launch vehicles.
The ITM of the NASU and SSAU holds leading positions in Ukraine and abroad in scientific research aimed at solving various problems of the dynamics of liquid-propellant launch vehicles and their subsystems, including the problems of ensuring the POGO stability of multi-stage liquid-propellant launch vehicles. The scientists of the department developed a linear theory of the POGO stability of liquid launch vehicles and created a non-linear theory of the POGO oscillations of liquid launch vehicles, which have no analogues in Ukraine and abroad. The most important component in these developments was the inclusion of cavitation in liquid propellant rocket pumps based on the theory of low-frequency cavitation self-oscillations created in the department for pumping power systems for liquid propellant rocket engines. Due to such accounting for cavitation, these developments allow us to make reliable forecasts of the POGO stability of liquid launch vehicles.
In world practice, the analysis of the POGO stability of liquid launch vehicles is performed only in a linear formulation using the results of preliminary expensive experimental work. It is based on the study of the linear dynamic system “LPRE – LV shell”, which describes the interaction of POGO oscillations of the LV shell and low-frequency processes in the LPRE, and the fact of stability or loss of stability of the system is predicted.
With the development of the linear theory of the POGO stability of liquid launch vehicles, the following important scientific and methodological developments were obtained.
- A method has been developed for predicting the dynamic characteristics of LPREs along the channels of the POGO stability of liquid launch vehicles, taking into account cavitation phenomena in screw centrifugal pumps, which allows reliable prediction of the dynamic characteristics of LPREs. Such forecasting is central to the theoretical analysis of the POGO stability of liquid launch vehicles. The figure shows that taking into account cavitation phenomena in pumps in a mathematical model of the dynamics of the RD-170 engine made it possible to obtain a satisfactory agreement between the calculated and experimental dynamic characteristics of this engine.
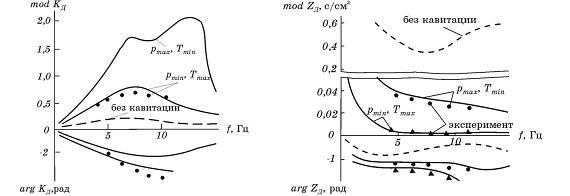
- A method of transferring boundary conditions to calculate the amplitude-phase frequency characteristics of power systems for liquid propellant rocket engines is proposed, which generalizes the impedance method to the case of multidimensional and distributed external influences.
- A method has been developed for multicriteria optimization of axial screw front-loading LPRE and POGO vibration dampers, which allows determining acceptable reserves of POGO stability of liquid launch vehicles.
- A procedure has been developed to analyze the interaction of POGO vibrations of the LV shell and low-frequency processes in the marching rocket engine during the flight of a liquid-propellant LV. The technique allows you to determine the complex eigen frequencies and modes of oscillation of the multi-circuit dynamic system “LPRE – LV body” and its subsystems; diagnose the stability of this system in relation to various types of low-frequency oscillations; to investigate the influence of individual subsystems on the parameters of the oscillatory process in a multi-circuit system, including the multi-frequency instability of this system.
- A procedure has been developed to determine the characteristics of natural POGO vibrations (natural frequencies, shapes, generalized masses and decrements) of a multi-stage liquid launch vehicle housing, taking into account the dissipation of vibrational energy of structural elements and liquid fuel in fuel tanks.
- Using the finite element method and modern computational tools, a theoretical forecasting method for dynamic loads on the upper stages of liquid launch vehicles with a complex spatial configuration of the fuel compartments and spacecraft (SC) in the process of putting them into working orbits has been developed. The methodology allows one to obtain quantitative estimates of the influence of the design features of the fuel compartment of the upper stage of the launch vehicle (a combination of the surfaces of the shell structures of its tanks, the presence of additional cylindrical inserts in the tanks) on the parameters of the natural POGO oscillations of the stage. This technique has no analogues in Ukraine and is the basis for performing theoretical predictions of dynamic loads on the design of the upper stages of liquid launch vehicles and spacecraft in the process of putting them into working orbits.
For several years, the department conducted research aimed at obtaining fundamental ideas about the laws of occurrence and development of POGO oscillations of liquid launch vehicles, which are considered as multidimensional nonlinear non-stationary systems “LPRE – LV body.” A nonlinear theory of POGO vibrations of liquid LV was created, which makes it possible to determine the magnitudes of the amplitudes of POGO vibrations of liquid LV. In the end, it is precisely the magnitudes of the POGO vibrations of liquid launch vehicles that should serve as the basis for decision-making on special measures to ensure the POGO stability of liquid launch vehicles. When creating a nonlinear theory of the POGO stability of liquid launch vehicles, the following basic scientific and methodological developments were obtained.
- The basic nonlinearities of the links of the dynamic system “LPRE – LV body” and their influence on the limitation of the amplitudes of POGO vibrations are studied. It is shown that the most significant nonlinearities that limit the amplitudes of POGO vibrations are the nonlinearities of the characteristics of the LRE and, above all, the characteristics associated with cavitation phenomena in screw centrifugal pumps.
- A procedure has been developed for the approximate determination of the amplitudes of POGO self-oscillations in the nonlinear system “LPRE – LV body” with “frozen” coefficients, which is based on the use of harmonic linearization methods. The technique allows you to determine the amplitudes of the oscillations, which can serve as an upper estimate of the amplitudes of the POGO vibrations of the non-linear non-stationary system “LPRE – LV body”.
- A method for calculating transients and steady motions in the “LPRE – LV body” system with a hierarchy of characteristic times and smooth nonlinearities based on the separation of motions in the “fast” subsystem (LPRE) and in the “slow” subsystem (elastic LV body) and using methods averaging, harmonic balance and continuation by parameter.
- The research has been conducted of the influence of damping oscillations of liquid fuel in tanks and elastic vibrations of the design of the LV on its POGO stability and the possibility of ensuring the POGO stability of the launch vehicle by increasing the damping of individual dynamic links of its housing.
- New effective methods and means have been developed to eliminate POGO vibrations of liquid launch vehicles: fundamentally new dampers of POGO vibrations of liquid launch vehicles are proposed and experimentally developed, which do not contain moving parts, automation elements and are more efficient than gas-liquid dampers; it substantiates the possibilities of ensuring the POGO stability of liquid launch vehicles without installing dampers of POGO vibrations, for example, by selecting parameters and changing the design of screw transfer pumps of mid-flight engines of the first stages of liquid launch vehicles.
On the basis of the developed linear theory of POGO stability of liquid launch vehicles and the created nonlinear theory of POGO vibrations of liquid launch vehicles, effective methods to analyze the POGO stability of launch vehicles that have no analogues in Ukraine and abroad have been developed. These methods were used to theoretically analyze the POGO stability of LVs for various purposes, created at SE “Yuzhnoye” and other organizations of the former USSR. The obtained calculation results made it possible to take effective practical measures to ensure the POGO stability of these LVs.
Employees of the department actively participated in the scientific and technical support for the development of the Zenit launch vehicle and its modifications, and, above all, in solving the problem of ensuring the POGO stability of the Zenit launch vehicle. This direction of the department’s activity was a priority at all stages of development of the launch vehicle. A large amount of work was carried out on a theoretical analysis of the POGO stability of the Zenit LV at different stages of development and the corresponding technical proposals were made that were implemented.
In 1981, in a short time, an analysis was made of the POGO stability of a military liquid rocket, which was developed under the guidance of Academician V.M. Chelomey. From a theoretical point of view, the loss of the POGO stability of the rocket during its launches to the maximum range was explained. It should be noted that the results of calculations performed for this LV demonstrated the fundamental importance of taking into account cavitation phenomena in liquid propellant rocket pumps in a theoretical analysis of POGO stability. Relevant recommendations were issued on the effective elimination of POGO oscillations in a rather simple way that does not require the development of special measures to stabilize the LV.
Mathematical simulation of the POGO oscillations of the RS-20 and 11K68 launch vehicles was carried out, satisfactory agreement was obtained between the calculated and experimental values of the amplitudes of the POGO oscillations of these launch vehicles on the active part of their flight during the operation of the first stage rocket engine.
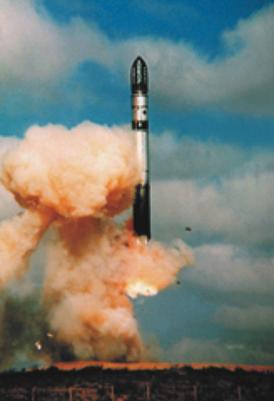
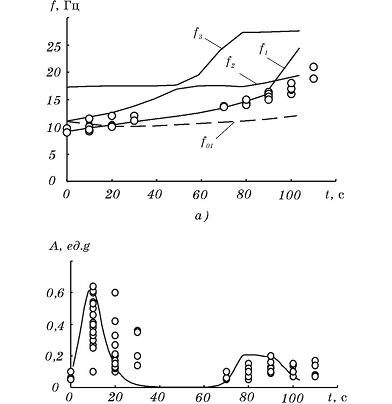
Theoretical forecasts of the POGO stability of Zenit-2SL and Zenit-3SL (as part of the Sea Launch program), Zenit-2M and Zenit-3SLB (as part of the Ground Launch program”). It should be noted that the theoretical forecast of POGO stability of the Zenit-2M and the Zenit-3SLB was carried out in the interests of the National Space Agency of Ukraine and by decision of the Council of Chief Designers in the “Yuzhnoye” Design Office. Practical recommendations have been developed to ensure the POGO stability of these LVs. The results of theoretical predictions were confirmed by the data of flight design tests of the LV.
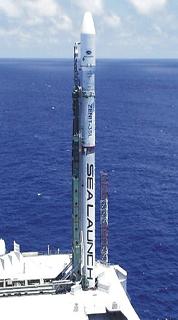
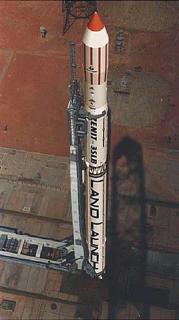
A theoretical analysis of the dynamic properties of “Antares” launch vehicle, which was developed on the instructions of Orbital Sciences Corporation (USA), is carried out. The main design of the first stage of the rocket was developed at the “Yuzhnoye” Design Office and manufactured at the Yuzhny Machine-Building Plant. A.N. Makarova in collaboration with a number of other Ukrainian enterprises. As a result of the analysis, the possibility of losing POGO stability of Antares LV was established and practical recommendations to ensure its POGO stability, which were implemented by Orbital Sciences Corporation, were proposed. In recent years, a number of successful launches of “Antares” LV have been carried out.
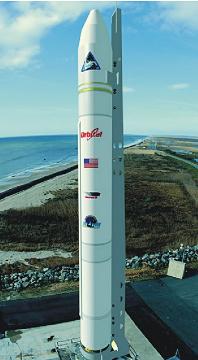
A theoretical forecast is made of the POGO stability of the Cyclone-4 LV and dynamic loads on the launch vehicle and spacecraft designs on the active part of the flight during the operation of the first stage rocket engine.
Scientific and methodological support was formed and a theoretical forecast was made for the POGO stability of new liquid space rockets at the stage of their preliminary design: tandem layout launch vehicles “KSLV-II” and “Mayak L3.0” (light class), launch vehicles of the bundled layout “Mayak T3 .0 “(heavy class). The main parameters of the POGO vibration damping system are determined to ensure the POGO stability of launch vehicles in the active part of the flight. Practical recommendations have been developed and sent to the Yuzhnoye State Enterprise to solve the problem of ensuring the POGO stability of these launch vehicles.
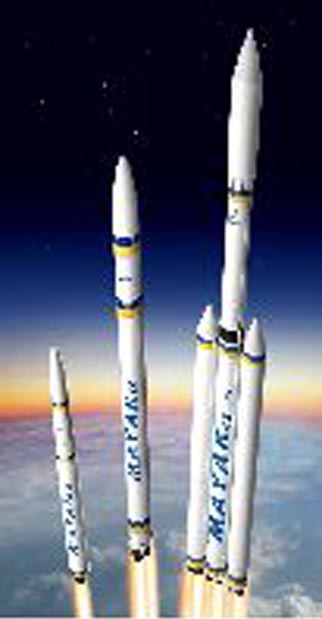
The development of fundamentally new dampers to provide liquid-propeller launch vehicle pogo stability
For the first time in the world’s space engineering of heavy and superheavy liquid-propellant launch vehicles practice there was created a fundamentally new and promising class of small dampers of pogo oscillations – hydrodynamic and thermodynamic efficiency of which is significantly higher than those of gas-liquid ones. In the hydrodynamic damper to obtain high ductility necessary for the pogo stability of LV, the supercavitation phenomenon is used, and in thermodynamic damper – thermodynamic effects in two-phase vapor-liquid media near the saturation line. The hydrodynamic damper passed a full cycle of experimental testing, was installed on the “Zenit” LV and provided its pogo stability.
- In the hydrodynamic dampers, the phenomenon of supercavitation is used to obtain the great compliance necessary to ensure the POGO stability of the LV, and the thermodynamic effects in the two-phase vapor-liquid medium near the saturation line are used in the thermodynamic damper. The hydrodynamic one went through a full cycle of experimental testing, was installed on the Zenit launch vehicle and ensured its POGO stability.
- The Damper-M bench was designed and created for dynamic testing of damping devices, the systems of which simulate the operating conditions of the damper, including on cryogenic liquid.
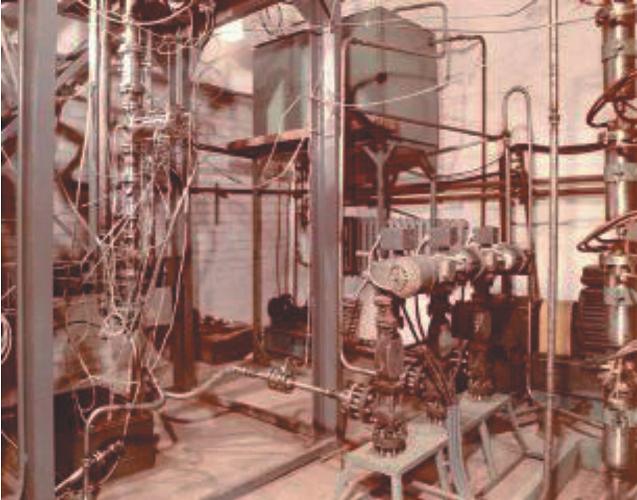
A series of theoretical and experimental studies of the dynamics of nonequilibrium thermodynamic processes of liquid evaporation and vapor condensation in two-phase vapor-liquid flows has been performed. The results obtained allowed us to conclude that it is advisable to use the dynamic properties of two-phase vapor-liquid media for the development and creation of fundamentally new highly effective means of vibration protection of various technical objects and systems.
The Collective Use Centre
In accordance with the Decree of the Presidium of the National Academy of Sciences of Ukraine of 27.03.08 # 174 with a view to the most rational use of unique scientific equipment at the Institute of Technical Mechanics there was created the Collective Use Centre. The main objective of the Centre is granting the NAS researchers the opportunity to conduct research using the equipment that is serviced by qualified staff.
The Centre’s equipment includes a unique bench, designed to conduct static, dynamic and strength tests of materials, structures and mechanical systems, servo-hydraulic plant “HYDROPULS” by the company INSTRON SCHENK TESTING SYSTEMS (Germany). The “Hydropuls” plant allows the study of the test object in a wide range of amplitude-frequency harmonic vibrations, deterministic and random perturbing influence. The frequency range of the disturbance is from 0.05 Hz to 80 Hz. The test object may have a mass of up to 3200 kg under dynamic loading and up to 4000 kg under static loading.
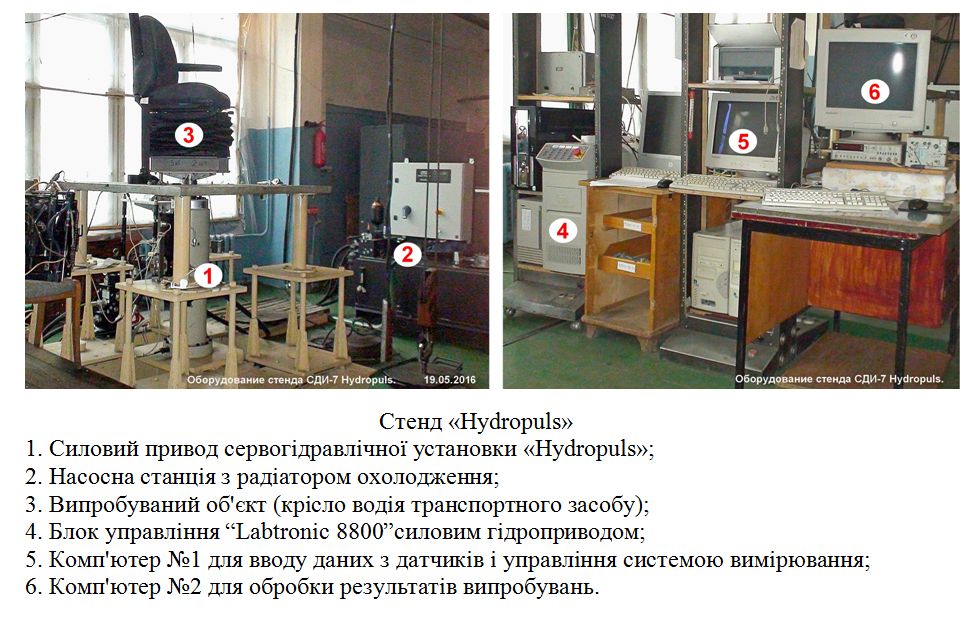
- The actuator of servo-hydraulic plant “Hydropuls”;
- Pumping station with the radiator cooling;
- The test object (vehicle driver seat);
- The “Labtronic 8800” power hydraulic drive control unit;
- Computer №1 to input data from the sensors and the measurement system control;
- Computer №2 for processing test results.
Vibration Protection Systems Dynamics
- A new pneumatic system for protecting the Sich-2M spacecraft from longitudinal vibrational loads when it is put into working orbits is proposed. This vibration protection system belongs to the type of autonomous passive systems and is not connected with the LV control system. The main component of the vibration protection system is an elastic-dissipative module. To ensure one-dimensional movement of the design of the vibration protection system along the longitudinal axis of the pH, guide elements are used. Mathematical modeling of the low-frequency dynamics of a vibration protection system with a spacecraft is performed. It is shown that the installation of a vibration protection system between the upper stage of the launch vehicle and the spacecraft provides a reduction in the level of longitudinal vibrational loads on the Sich-2M spacecraft in the frequency range from 5 Hz to 100 Hz two times or more, satisfying the requirements of the Technical Assignment. The installation of the proposed vibration protection system of the spacecraft on launch vehicles will significantly expand the capabilities of launching spacecraft for various purposes into working orbits and increase the competitiveness of launch vehicles in the global space services market.
- The fundamentals of the theory and design of fundamentally new highly efficient thermodynamic and pneumatic vibration protection systems with quasi-zero stiffness on the working section of a static characteristic are developed. The proposed designs of vibration protection systems make it possible to provide an ultralow natural frequency of vibrations and do not require the installation of a hydraulic shock absorber to dissipate the vibration energy.
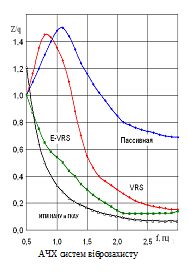
- The design of the vibration protection system for the driver’s seat of various purposes has been developed to protect against shock and alternating loads arising from movement. Prototypes of such chairs were made, their static and dynamic tests were carried out. It has been established that the developed vibration protection systems in terms of their static and dynamic characteristics (quasi-zero stiffness at the working section of the static characteristic, natural vibration frequency of the protected object) fully meet the requirements of European standards and are not inferior to the best world analogues of passive, semi-active and active vibration protection systems. In fig. amplitude-frequency characteristics (AFC) of vibration protection systems developed by the ITM of the NASU and SSAU, passive, semi-active (VRS) and active (E-VRS) firms Searc (USA) are presented. It can be seen that the vibration protection system developed by the ITM of the NASU and SSAU has the best dynamic characteristics. In fig. The ITM of the NASU development chair with a vibration protection system and possible options for its use are shown.
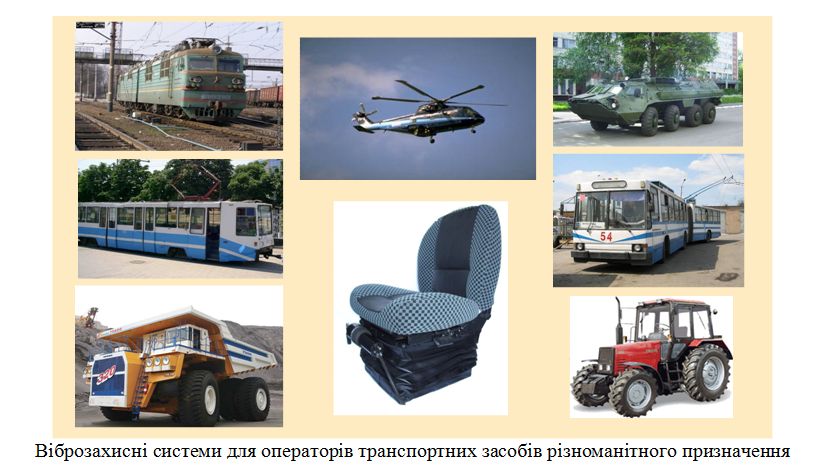
The design was developed and experimental samples of new pneumatic car suspensions were manufactured (see Figure), which, after determining the static and dynamic characteristics, were installed on a serial car, and sea trials were conducted. The decrease in the natural frequency of oscillations of the sprung mass of the car with new suspensions ensured a decrease in the human susceptibility to vibrations by 3 times for asphalt concrete roads and 6 times for roads with cobblestone-asphalt surface.
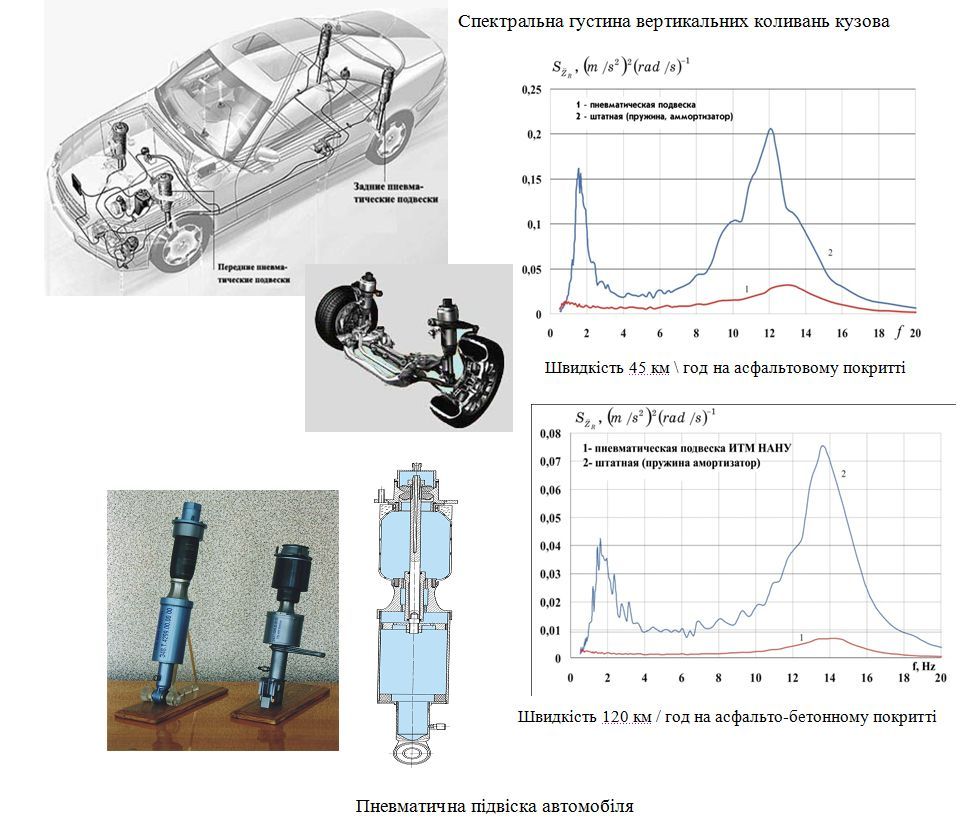
The characteristics of the new pneumatic suspensions satisfy the requirements of smoothness and stability of movement of a high-class car. The cost of these pendants is comparable to the cost of traditional pendants made on the basis of metal elastic elements and hydraulic shock absorbers.
Dynamics of hydraulic systems with cavitating flow restrictors
- Systematic theoretical and experimental studies of high-frequency high-amplitude oscillations of fluid pressure in hydraulic systems with cavitating local hydraulic bearings have been performed. A fundamentally new generator of fluid pressure fluctuations is developed – a cavitation oscillation generator, which allows you to turn a stationary fluid flow at the inlet of the generator into a pulsating high-frequency high-amplitude flow at the outlet of it. The oscillation generator does not contain moving parts and does not require the supply of additional energy. The possibilities of using such pulsating fluid flows to create new promising, high-performance, environmentally friendly technological processes in various industries: emulsification, dispersion, surface cleaning, and well drilling, have been investigated. Technological developments are protected by more than thirty copyright certificates.
- A pulsed cavitation installation for dispersing various suspensions has been developed. The installation passed industrial tests at the Dnepropetrovsk paint and varnish factory in the workshop for the preparation of paint pastes and at the Crimea TITAN Production Association in the workshop for the production of titanium dioxide. The installation made it possible to replace expensive imported equipment, ensure the necessary degree of dispersion of suspensions, and reduce the specific energy consumption for manufacturing a unit of production by 4-6 times.
- Descaling units were created with pulsating jets during hot rolling of metal, which were introduced at the Vyksa Metallurgical Plant, the Orsk-Khalilovsky and Kommunarovsky Metallurgical Combines, and the Zaporizhstal Works. Settings allow 2-5 times reduction of metal scrap (due to press-fit of the scale) compared to steady-jet descalers.
- The study of the outflow of a cavitating high-pressure hydroabrasive pulsating jet and of the conditions of its generation has made it possible to develop and implement advanced technologies and plants for cavitation pulse hydroabrasive treatment (CPHAT) of different surfaces, including metal surfaces of rocket structures. The design and engineering solutions of CPHAT are based on more than 25 inventions.
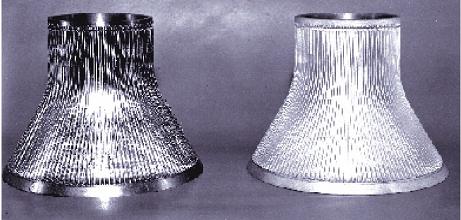
A numerical simulation of the unsteady fluid flow in a hydraulic system with cavitating elements is carried out on the basis of a mathematical model that includes the complete Navier – Stokes equations and the barotropic equation of state of a vapor-liquid mixture. The calculation mode reproduces the cavitation self-oscillations in the specified hydraulic system. A satisfactory agreement was obtained between the calculated and experimental values of the frequencies and amplitudes of cavitation self-oscillations. The results of numerical simulations allow us to expand existing ideas about the phenomenon of the generation of high-frequency oscillations of fluid pressure in hydraulic systems with cavitating local hydraulic bearings. They are also of practical importance in the creation of new and intensification of existing technological processes in various industries based on the use of pulsating cavitational fluid flows.
An important scientific direction of the work carried out in the department is to solve the problem of grinding solids in a liquid medium based on hydrodynamic studies of new technical devices with cavitating elements. An experimental cavitation-impulse installation for producing finely dispersed media was developed and created, which is primarily intended for the preparation of water-coal fuel by grinding coal – the main energy resource of Ukraine and coal sludge concentrates. Technical devices that implement the process of cavitation-pulsed grinding of solids and ensure its effectiveness, have been improved. The work performed is aimed at creating an environmentally friendly technology for the preparation and burning of a coal-water mixture, an important energy-saving technology, the introduction of which will help to reduce dependence on external energy supplies. The technology will significantly reduce energy consumption in the manufacture of finely dispersed media in comparison with other grinding methods. The obtained scientific and technical solutions, developed technologies and created cavitation-pulse installations can be used in many industries of Ukraine where the use of finely dispersed media is necessary. Along with the production of coal-water fuels, such industries include the food industry, paint and varnish production, powder metallurgy, etc.
Environmentally-friendly technology for the preparation and burning of fine-particle coal-water fuel
- A fundamentally new technology for the production of finely dispersed coal-water fuel (CWF) has been proposed. An experimental cavitation-pulse plant has been developed, in which a new cavitation-pulse dispersant (a system of cavitation-pulse oscillation generators) and a fuel feed system to the nozzle of the burner device of a thermal boiler are integrated (see Fig.). The plant allows the use of coal slurry concentrates and coal of various grades with a fractional particle size of class 0 – 3.0 mm for the preparation of CWF. The proposed cavitation-pulsed technology for producing coal-water fuel has no analogues and makes it possible to obtain coal-water fuel with a coal concentration of more than 70% and a degree of dispersion of 90% less than 50 microns with a significant (several-fold) reduction in specific energy costs per unit of production compared to traditional technologies, based on the use of ball and bead mills.
- For efficient flaring of coal-water fuel, a special burner device for a heat boiler was developed, manufactured and experimentally tested, including the original design of a nozzle for cutting coal-water fuel, a primary air supply system and an adjustable secondary air supply system with preheating to 700 ° C. Full-scale tests of the burner device in the long-term flare mode showed its high efficiency in terms of the completeness of combustion of coal-water fuel obtained both on the basis of coal and on the basis of sludge concentrate.
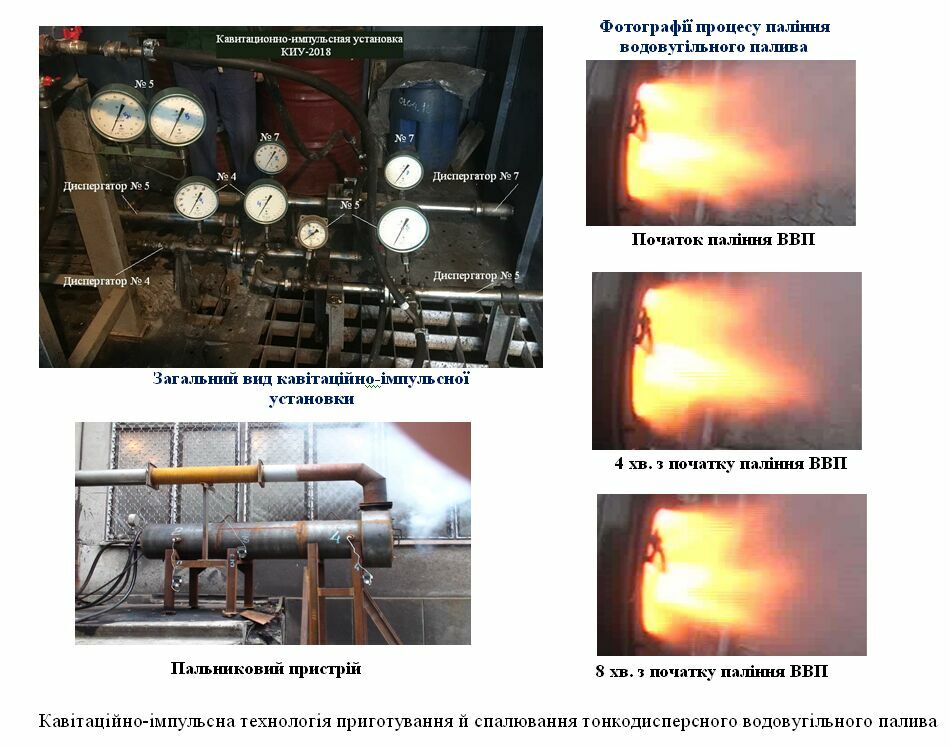
Practical recommendations on the modernization of “E-series” thermal boilers for the development of technological procedures for their transfer by gas or fuel oil burning technology to the combustion of coal-water fuel have been issued.
An environmentally friendly technology for the preparation and burning of finely dispersed coal-water fuel is the most important energy-saving technology, which significantly increases the efficiency of use of fuel resources of Ukraine.
Impeller machine gas-dynamics
- The challenge of improving the quality of aerodynamic design of aircraft gas turbine engine (GTE) elements is relevant both for Ukraine and for other countries that develop aviation equipment. The main way to solve this problem is to use modern effective scientific developments. In this regard, scientific and methodological support was developed, which has no analogues in Ukraine, for solving the problems of aerodynamic improvement of the shape of the blade crowns of gas turbine engines in two-dimensional and three-dimensional formulations. This software was used at one of the enterprises – aircraft engine developers – in the Ivchenko-Progress state enterprise (Zaporizhzhya), which is one of the leading enterprises in the world in the design and development of the input device, fan impellers and centrifugal stages of gas turbine engines. This has made it possible in some cases to reduce the time needed to create models of aircraft (which are currently being mass-produced) due to a fairly accurate prediction of the degree of aerodynamic perfection of the shape of the interscapular channels of axial and centrifugal compressor stages at the early stages of design.
- The main components of the original scientific and methodological support for the numerical solution of the inverse problems of the gas dynamics of blade vanes of compressors of aircraft gas turbine engines using modern methods of numerical simulation of transonic inviscid gas flows, have been developed. This development will be of key importance in solving the problem of aerodynamic design of compressor blades for the aerodynamic design of the aircraft engine countries.
- Based on an integrated approach using gas flow models of various levels, the urgent problem of aerodynamic optimization of grating profiles has been solved. The results can be used in the aerodynamic design of the rims of the compressor blades of aircraft gas turbine engines.
- Software and methods has been developed to calculate a turbulent boundary layer and predict its separation on compressor grating profiles. These have been transferred to the Ivchenko-Progress State Enterprise for use at the stage of aerodynamic design of the blade crowns of aviation gas turbine compressors.
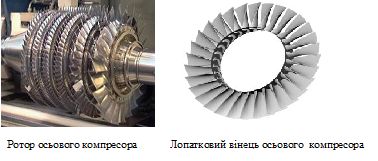
- Software and methods have been developed and the stress-strain state of the compressor rim blade was calculated using the OpenFOAM numerical modeling platform.
- Modern methods of aerodynamic improvement of the shape of interscapular channels of aviation gas turbine compressors have been developed based on numerical modeling of spatial turbulent gas flows.
The development results were used and can be further used in the “Ivchenko – Progress” State Enterprise for optimization of the blade crowns of aircraft gas turbine engine compressors at the design stage.
The challenge of intensification of the drilling process in solid rocks
The challenge of intensification of the drilling process in solid rocks is relevant not only in Ukraine and the CIS countries, but also in the USA, Canada, Norway and other countries. Theoretical and experimental studies have been carried out on the feasibility of implementing one of the most promising ways to solve this problem – the method of creating axial dynamic loads (POGO vibration accelerations) on a rotary rock cutting tool of a drill using an original, unparalleled, cavitation hydraulic vibrator developed in the department. The high-frequency hydraulic vibrator does not contain rotating moving parts, does not require reconfiguration in depth and additional energy supply (it uses only part of the energy of the flushing fluid flow in the drill). The simplicity of the design and operation of the hydraulic vibrator significantly increases the reliability of the drill with the cavitation hydraulic vibrator.
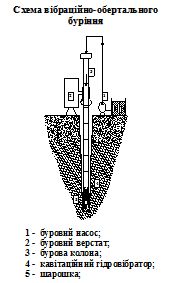
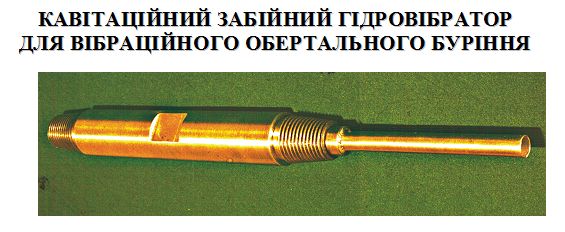
The development of theoretical and design basics for report reduction devices for small-arms silencers
Studies have been conducted on the creation of devices to reduce the report level – silencers for light firearms of caliber 5.45 – 12.7 mm.
Software and methods has been developed to calculate the characteristics of the gas flow in the RRD, which allows the selection and calculation of the design schemes of devices that provide the greatest efficiency in reducing the report.
The RRDs are designed to eliminate injuries to the shooter’s hearing organs, reduce sonic visibility, suppress a flash of a shot, reduce recoil, increase accuracy and accuracy when firing in combat operations, as well as training and training firing, and reduce environmental pollution.
The created devices have advantages in comparison with analogues in basic operational characteristics.
The analysis of the effectiveness of the RRD is carried out depending on the number of cameras and their location, the number of holes, their configuration.
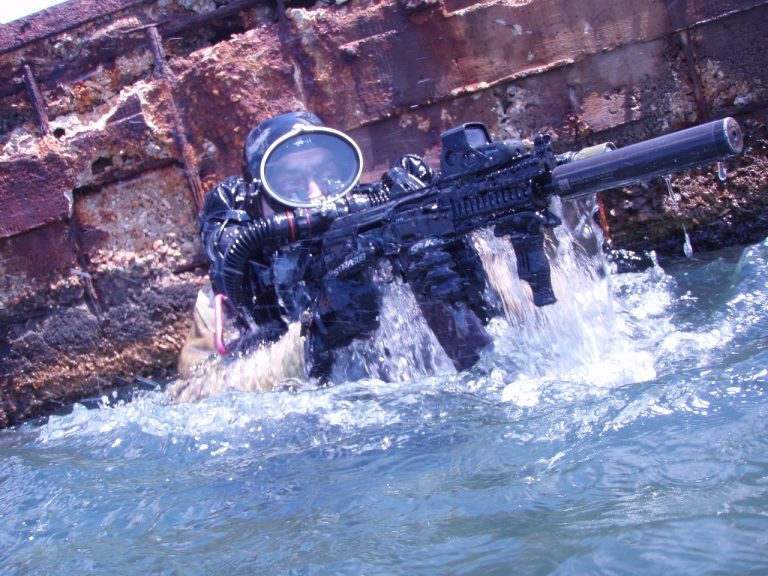
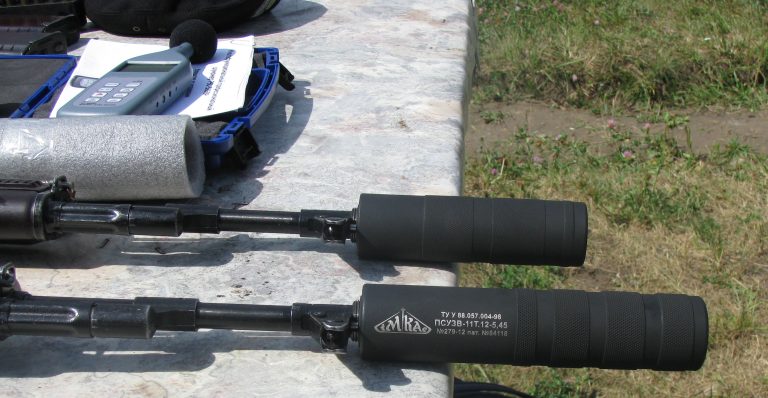
Experimental studies have been carried out to identify the gas-dynamic picture of the flow in the cavity of the RRD using optical imaging tools.
A method has been developed to determine the effectiveness of reducing the sound level of a RRD shot using compressed gas and an installation for its implementation.
The technical conditions for RRD, TU U 88.057.004-98 and TU U 88.057.005-98, programs and test methods, and parameter measurements were developed and approved.
The development and testing of the RRD were carried out jointly with IMKAS and divisions of the Security Council of Ukraine and the Ministry of Internal Affairs of Ukraine, as well as with domestic manufacturers of small arms.
Devices for report reduction have the following advantages compared to well-known analogues:
– they are manufactured from corrosion-resistant steel, aluminum and titanium;
– their life is at least 10,000 shots, which corresponds to the life of the barrel of the weapon;
– the possibility of use in any operating conditions;
– no effect on the speed of the bullet;
– the ability to fire supersonic cartridges as single shots and automatic fire;
– the effectiveness of sound pressure level reduction is not less than 25 – 34 dB.
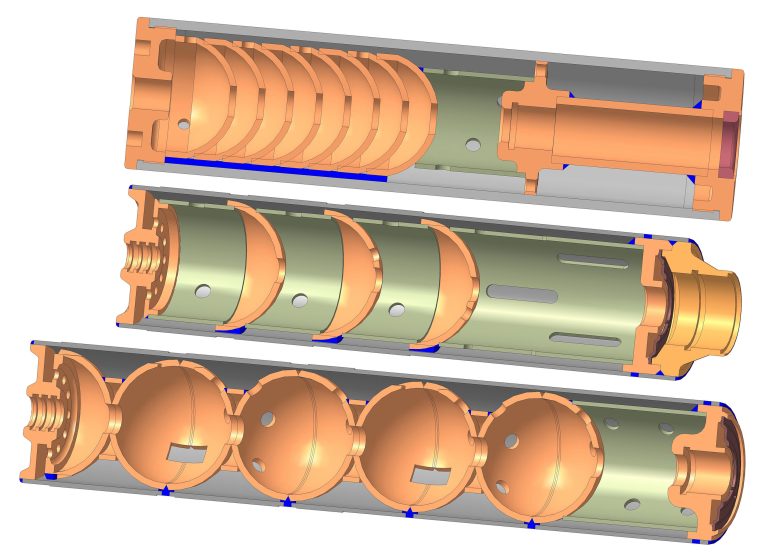
Based on the results of the development of the RRD designs and research, a monograph and a textbook for the training of specialists were published, 36 articles were published in scientific and technical journals, the work is presented by 4 reports at international scientific and technical conferences. The RRD designs are protected by 29 patents of Ukraine.
The manufactured devices are used in the power structures of Ukraine.
Development materials are used in the educational process of the Dnipropetrovsk National University. O. Potter. The textbook “Silent automatic firearms” was published (Dnepropetrovsk, Institute of Technical Mechanics of the National Academy of Sciences of Ukraine and the National Aviation Administration of Ukraine ART-PRESS, 2011. – 346 p.)
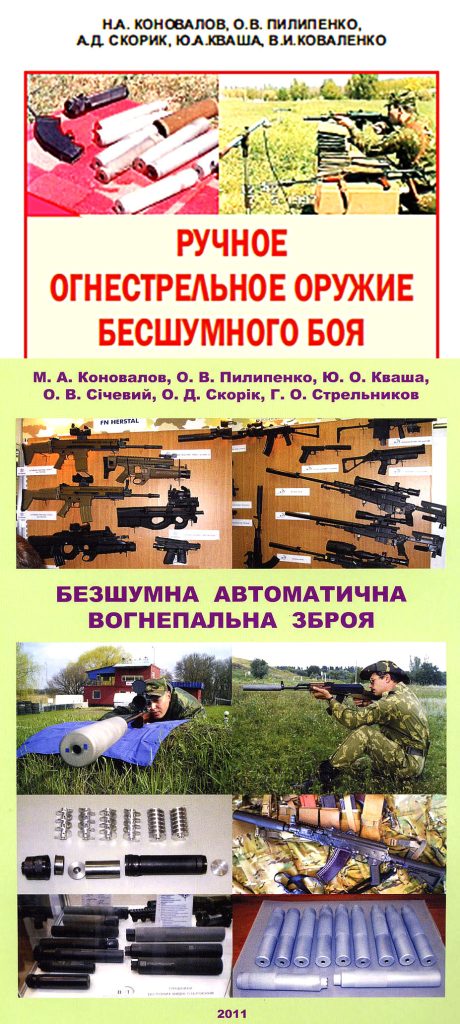
The main research results are published in numerous articles and monographs, of which the most fundamental are:
- Pylypenko V.V. Cavitation Self-Oscillations and hydrosystems dynamics / V.V. Pylypenko, V.A. Zadontsev, M.S. Natazone. – M.: Mashinostroyeniye, 1977. 352 pp.
- Pylypenko V.V. Cavitation Self-Oscillations / V.V. Pylypenko. – Kiev: Naukova Dumka, 1989. 316 pp.
- N. A. Konovalov, O. V. Pilipenko, A.D. Skorik, Yu. A. Kvasha, V.I. Kovalenko. Small arms silent battle. Dnepropetrovsk: Publishing House of the Institute of Tech. mechanics of the NAS of Ukraine and the Civil Aviation Administration of Ukraine, 2008. 330 pp.
The research works of the department scientists were awarded with the USSR State Prize in the field of science and technology (1990), the State Prize of Ukraine in the field of science and technology (1997. and 2005), and Prizes of the NAS of Ukraine named after M.K. Yangel (1983., 1989, 1998. And 2016 p.) and Prizes of the NAS of Ukraine named after O.K. Antonov (2004).
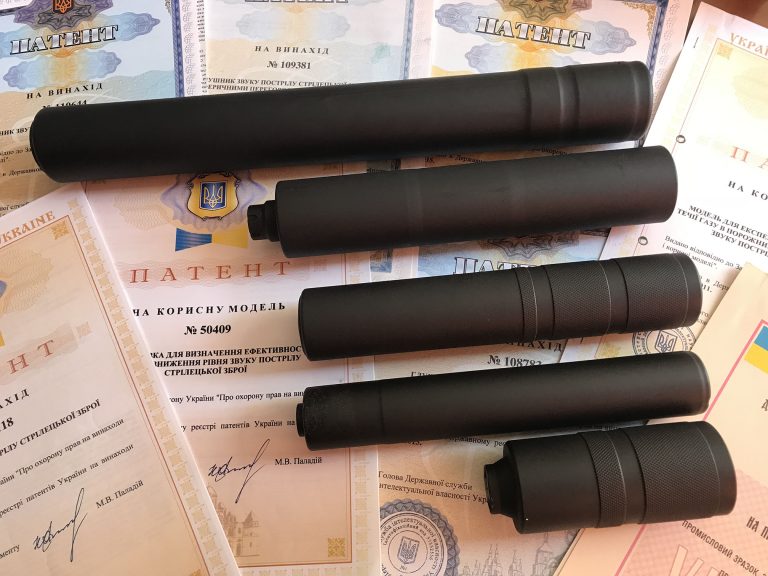
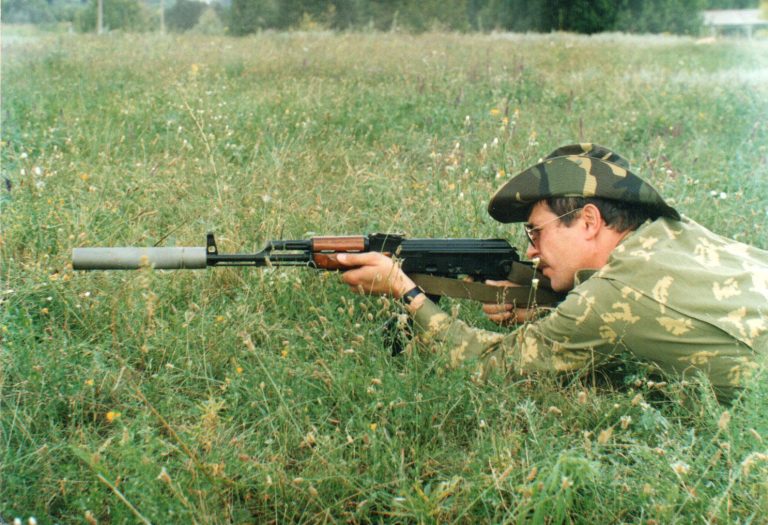
OFFICE ADDRESS: | Institute of Technical Mechanics , 15 Leshko-Popelya St., Dnipro, Ukraine, 49005 |
PHONE NUMBER: | +38-056-372-06-50 |
E-MAIL: | Office.itm@nas.gov.ua |