Head of department – D.Sc., Professor Nataliia S. Pryadko
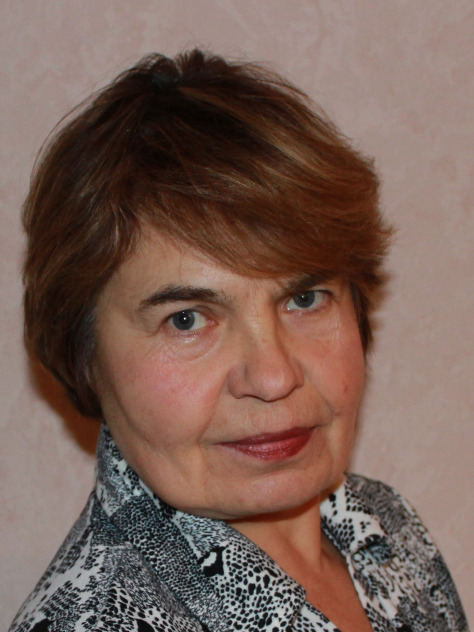
The department counts 13 employees, including 2 Doctors of Science, 5 PhDs.
Field of research – thermogasdynamics and heat-mass exchange in rocket and space engines, heat power and technological equipment; mechanisms, models and research methods of gas flow control characteristics in rocket engines and elements of gas-jet technological equipment; expanding the functionality and improving the performance of control systems for the thrust vector of rocket engines and the grinding process of bulk materials.
Rocket Engine Thrust Vector Control
The fundamental mechanisms of the perturbation of a supersonic flow by discrete and distributed sources of mass and heat, liquid and gas jets, solid obstacles, technological imperfections and erosive drifts on a streamlined surface have been revealed. Methods have been developed to calculate the local and integral, static and dynamic characteristics of the gas flow control process in the nozzle of a rocket engine. The methods are based on theoretical developments and experimental data obtained on unique research complexes created in the ITM. Studies of supersonic flow disturbances on models and full-scale engines have confirmed the developed physical and mathematical simulations. The research results created a scientific basis for the development of new technical solutions for the thrust vector control of traditional and new types of nozzles of rocket engines operating on liquid, solid and gaseous fuels.
Research on the control of supersonic flow of rocket engines has been conducted in close collaboration with the Yuzhnoye State Design Office . The thrust vector control system for rocket engines by injection into the supersonic part of the nozzle of fuel combustion products has been used by the Yuzhnoye State Design Office in a number of liquid and solid propellant rocket engines, in particular 15D12, 15D169, 11D25, RDTT 3D65, 15D206 liquid propellant engines.
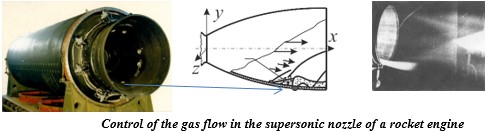
In the process of scientific support of their creation, the static, dynamic, heat-and-mass exchange and operational characteristics of the traction vector control systems and the engine as a whole (as an object of regulation) were studied, calculation methods and recommendations for the design and development of such engines were developed. A mathematical simulation of solid propellant rocket engine with chamber gas injection into the supersonic part of the nozzle as an object of regulation has been developed. The possibility and appropriateness of the programmed regulation of the second engine fuel consumption by the standard side-force controls (injection valves) are shown, which allows expanding the functionality of the solid propellant rocket engine and increasing its energy characteristics.
Created for the first time in the practice of rocket science, these engines made it possible to develop rocket stages unsurpassed to date by the high level of energy, dynamic, overall and operational characteristics.
Scientific support was provided at all stages of development of these engines, including flight tests. In particular, the results of studies of gas-dynamic control of the thrust vector were used to develop the conclusion of the state commission on determining the causes of the emergency flight design test of the rocket engine 11D25 of the Cyclone-3 rocket No. 40 L.
Further research in this area has proposed new methods, schemes and devices to control the thrust vector of liquid rocket engines of stages of launch vehicles and upper stages of spacecraft relative to the engines of upper stages of rockets (such as RD11D25, RD861K) and upper stages of spacecraft, which are characterized by high degrees gas expansion in the nozzle.
A new concept has been developed to control the thrust vector of a rocket engine – a combination of mechanical (swinging engine or nozzle) and gas-dynamic (disturbing supersonic flow in the engine nozzle) systems. An advantage of the new concept is the possibility of creating an unlimited amount of programmed control effort and parry with a high frequency of small-sized flight disturbances with virtually no loss of engine specific impulse. This significantly increases the reliability of the control system (due to duplication). A new concept has been developed to control the thrust vector of a rocket engine – a combination of mechanical (swinging engine or nozzle) and gas-dynamic (disturbing supersonic flow in the engine nozzle) systems. An advantage of the new concept is the ability to create an unlimited amount of software control effort and parry with a high frequency of small-sized flight disturbances with virtually no loss of specific engine impulse. This significantly increases the reliability of the control system (due to duplication).
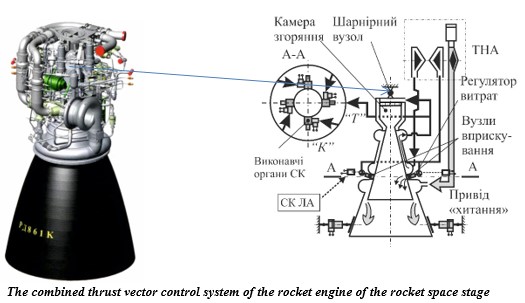
The advantage to control the thrust vector by injection into the nozzle of the oxidizing component of the fuel, in particular through a solid interceptor, which extends into the flow, is shown. The operability of new circuits and designs of interceptor devices is confirmed by their purges in cold air and fire tests as part of the rocket engine and solid propellant rocket engine.
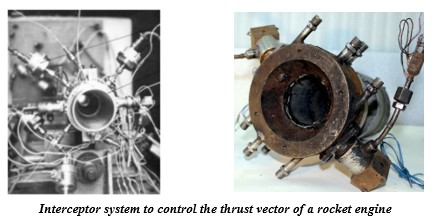
New nozzle configurations
New nozzle configurations and software have been developed to calculate their characteristics. The promising design of the plate-shaped nozzle with a flowing central body, developed at ITM, is shown, which allows to reduce the longitudinal dimensions of the nozzle and to ensure the control of the thrust vector of the engine, both in terms of magnitude and direction.
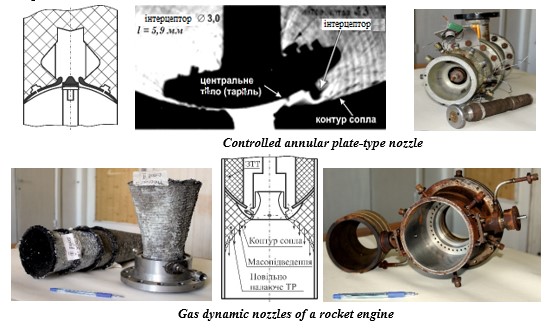
Nozzles for dense configurations of multi-stage rockets
The gas flow in a non-standard nozzle of a rocket engine with a bell-shaped nozzle has been studied. The influence of the shape of the nozzle and the conditions of use of the shortened nozzle on its characteristics has been established. The results of calculations have been compared with experiments – cold air blowing of models of a similar shortened nozzle. It is shown that the flow in the nozzle includes supersonic and subsonic flows that interact with recirculation regions and represent a complex wave structure.
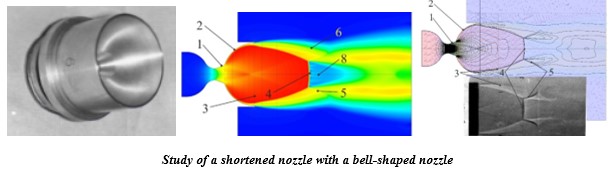
Detonation engines
Fundamentally new rocket engines with the detonation process of fuel combustion in the chamber have been developed and researched. The advantages of detonation devices to solve new tasks in rocketry and space and other fields of technology are shown, in particular to increase the efficiency of thrust vector control when solving various applied issues of separating and removing the fairing of a rocket stage, generating a working body for spacecraft control systems, and the sequentially burning design of a multi-stage rocket etc.
On the basis of the conducted research, a new line of work is being developed using detonation rocket engines for the defense complex of Ukraine. These studies are due to the need to improve the energy and operational characteristics of special-purpose propulsion systems for promising rockets.
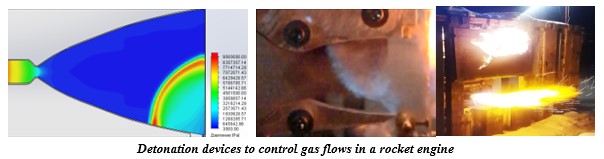
Technological processes
The processes of burning lump coal in a furnace with a circulating fluidized bed have been investigated jointly with the Yuzhnoye State Design Office. New methods are proposed for organizing a process above the bottom grate with gas-dynamic transportation and unloading of ash and slag waste to eliminate the diffuser effect leading to instability of the gushing layer during lump coal transportation.
The processes of fine purification of flue gases have been studied, the optimal hydrodynamic, geometric, structural and operational parameters of emulsifier devices have been determined. The results obtained on the improvement of the furnace for coal combustion and flue gas treatment were used in the modernization of Karagandaenergo, Alma-Ataenergo, in Ukraine Mironovskaya State District Power Plant and others.
New methods and devices for burning various fuels have been developed. These methods are based on an organized pulsating combustion mode and provide economic, environmental and operational advantages compared to existing ones. Experimental samples of burner devices have been developed, manufactured and tested for: OJSC “Azot” (Mariupol) – in relation to the combustion chamber of the nitrous gas heating system in the production of nitric acid; OJSC “Bagliikoks” and others.
The scientific basis of acoustic monitoring of fine grinding has been developed to identify technological modes of grinding and increase the efficiency of the process. Acoustic efficiency parameters and an optimality criterion for the operation of a jet mill have been established. The possibility of optimizing jet grinding of mineral raw materials based on the results of acoustic monitoring of the process is shown. Methods of visualization and optimization of grinding using information technologies have been developed. This made it possible to achieve the necessary technological indicators while reducing energy consumption and observing control dispersion.
The method of material dispersion control based on acoustic monitoring of the process has been substantiated. The “Granulometer” installation has been developed to determine the particle size distribution of materials in an energy carrier stream. The developed method for controlling the quality of the crushed product significantly (30 times) accelerates the process of determining the fineness of the finished product, allows to improve the quality of the finished product and reduce energy consumption when turning off the processing.
Based on the results of continuous monitoring of the working zones of the grinding plant, a model of the movement of mass flows in a closed cycle and changes in the granulometric composition of the input material from the loading hopper to the discharge of the finished grinding product has been created. An automatic system for controlling the productivity of the jet plant has been developed based on the control of its loading based on the results of acoustic monitoring of the working zones of the mill. The created hardware base for controlling the jet mill has been tested during experimental and industrial processes of grinding various materials.
All studies were tested in the industrial conditions of the Volnogorsk Mining and Metallurgical Combine.
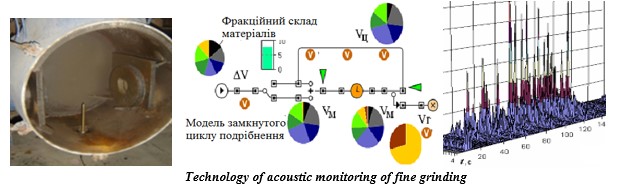
Complexes for the study of objects of rocket and space technology
The obtained results are based on theoretical studies and experiments based on the ITM of the National Academy of Sciences and the State Space Agency of Ukraine, which includes research complexes of thermogas dynamics of rocket engines and technological processes: high costs and pressure; gas dynamics of controlled flows; detonation devices; gas jet grinding transportation and drying of bulk materials; heat and mass tranfer.
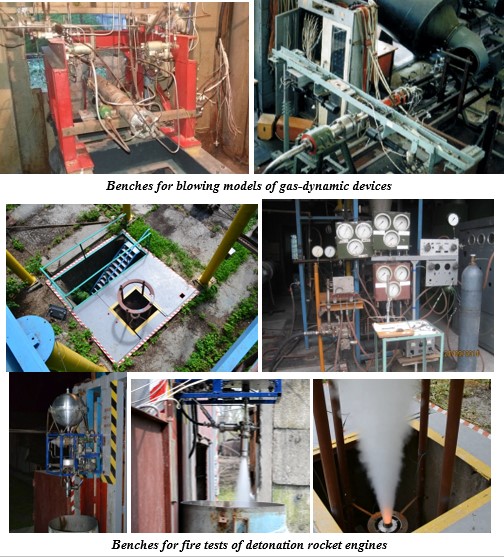
Complexes of technological process research
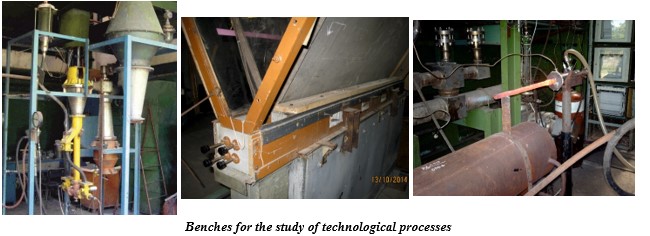
Based on the research results, new technical solutions have been developed, more than 100 of which are protected by copyright certificates and patents for inventions.
It should be emphasized, the great contribution to the research conducted by the head of the department Mykola Dmytrovych Kovalenko in 1971-2017. M. D. Kovalenko was the laureate of the State Prize of Ukraine for the development of the fundamentals of the gas-dynamic thrust vector control system for solid propellant rocket engines; Laureate of the National Academy of Sciences of Ukraine named after M.K. Yangel for the development of power plants that provide high performance aircraft; honored Worker of Science and Technology of Ukraine, holder of a number of medals and orders.
Modern experimental base of the department of thermogas dynamics of power plants
The experimental base of the department includes 5 operating benches for studying engine engineering problems and 2 operating benches for researching technological processes:
- “BPM” Bench for purging models of gas-dynamic devices
- Bench for fire tests of detonation rocket engines
- Vertical bench for fire tests of rocket engines
- “VM-50” Monofuel rocket engine fire test bench
- “VM-200” Modular bench for fire tests of rocket engines on monofuel with a hybrid pyrostarter
- “USI-20” bench (gas-jet grinder)
- “AEROFOUNTAIN” bench
The existing and planned experimental benches allow to fully study the problems of engine construction and the peculiarities of technological processes. Similar individual benches are used abroad, but there is nowhere a complex that would allow studying different types of detonation engines and technological processes.
Current cooperation
A number of works and studies have been carried out and are conducted in cooperation with leading institutions of the space and mining enrichment industry, universities and academic institutes: M. K. Yangel State enterprise Yuzhnoye Design Office, Vilnohorsk Mining and Metallurgical Plant, JSC “United Mining and Chemical Company”, NTU “Dniprovsk Polytechnic”, Oles Honchar Dnipro National University, Ukrainian State Chemical and Technological University, Kryvyi Rih Technical University, Ukrainian State University of Science and Technology and others.
Since 2017, the position of the head of the department is held by H. O. Strelnykov.
The results of the department’s work are summarized in monographs and articles:
- Kovalenko N.D. Perturbation of a supersonic flow during mass heat supply. Kiev: Naukova Dumka, 1980 .– 224 p.
- Kovalenko N.D. Unsteady Thermal Processes in Flying Vehicle Power Plants (in Russian) Kiev: Naukova Dumka, 1988. 224 pp.
- Kovalenko N.D. Supersonic Gas Flow Control in Jet Nozzles (in Russian) Kiev: Naukova Dumka, 1992. 208 pp.
- Kovalenko N.D. Gas-dynamics of Supersonic Truncated Nozzles (in Russian) Kiev: Naukova Dumka, 1993. 224 pp..
- Strelnikov G.A. Adjustable Short-length Supersonic Nozzles (in Russian) – Dnepropetrovsk: State University, 1993. 30 pp.
- Kovalenko N.D. Rocket Engine as an Executive Device of the Rocket Flight Control System (in Russian) – Dnepropetrovsk: Institute of Technical Mechanics of the NASU and the NSAU, 2004. – 412 pp.
- Pryadko N.S. Acoustic studies of jet grinding / LAP LAMBERT Academic Publishing. – 2013. – Saarbrucken Germany. – 172 pp.
- Pivnyak G.G., Pilov P.I., Pryadko N.S. Decrease of Power Consumption in Fine Grinding of Minerals// Mine Planning and Equipment Selection C Drebenstedt and R. Singhal (eds), Springer International Publishing Switserland 2014.–P. 1069 – 1079
- Pryadko N.S. Optimization of fine grinding on the acoustic monitoring basis// Power Engineering, Control & Information Technologies in Geotechnical Systems – Pivnyak, Beshta & Alekseyev (eds) 2015 Taylor & Francis Group, London, р. 99 – 108.
- Pryadko N.S. Application of information technology for decrease of fine grinding power сonsumption //Power Engineering, Control & Information Technologies in Geotechnical Systems – Pivnyak, Beshta & Alekseyev (eds) 2016 Taylor & Francis Group, London, р. 67 – 73
- Pryadko N.S., Ternova K.V. Acoustic monitoring of jet grinding // NAS of Ukraine, Institute of Technical Mechanics of NAS of Ukraine and SSA of Ukraine. — Kyiv : Akadem periodyka, 2020. — 192 p.
- Pryadko N.S. Information technologies for optimizing the fine grinding of materials // System technologies for modeling complex processes: a collective monograph, ed. prof. A. I. Mikhaleva. – ITM NASU and SSAU. – Dnipro. NMetAU-IVK “System Technologies”, 2016. – Pp. 463-499. – 608 p.
ARTICLES included in the scientific metric databases Scopus, Web of Science
1 Mladetsky I. K., Kuvaev I. G., Pryadko N.S. Control regularities of the useful mineral extraction from ore feed stream with ball grinding. Spectral analysis// Scientific Bulletin of National Mining University. – 2017. – № 6. – С. 132 – 138.
2 Mladetsky I. K., Kuvaev I. G., Pryadko N.S. The control regularity detection of the useful mineral extraction from the ore feed stream with autogenous grinding Part 1. Correlation analysis// Scientific Bulletin of National Mining University. – 2018. – № 2. – С. 98 – 106/
3 Muzyka L.V., Pryadko N.S., Strelnikov H.A.,Ternova K.V., Verhorobina I.V. Acoustic method of jet grinding study and control// E3S Web of Conferences 109, 00074 (2019) Essays of Mining Science and Practice 2019 р.1-11.
4 Muzyka L.V., Pryadko N.S., Strelnikov H.A., Grenev A.F Control of mass flow in jet mill on base of acoustic monitoring // Scientific Bulletin of National Mining University. – 2019.–№ 4. – Р. 5-10. https://doi.org/10.29202/nvngu/2019-4/3.
5 Bublikov A.V., Pryadko N.S., Pilov P.I., Papaika Yu. A., Ternova K.V. Automatic control of jet grinding on the basis of acoustic monitoring of mill operating zones // Scientific Bulletin of National Mining University. – 2021. – № 4. – Р. 29 – 34. https://doi.org/10.33271/nvngu/2021-4/029.
6 Pryadko N.S., Mladetsky I. K., Dzjuba S. Control characteristic accuracy of mineral processing technology parameters// E3S Web of Conferences 109, 00074 (2021) Essays of Mining Science and Practice 2021 р. 1-11.
7 Strelnіkov G., Ihnatiev O., Pryadko N., Ternova K. Efficiency of rocket engine thrust vector control by solid obstacle on the nozzle wall // Proc I MechE Part G: J Aerospace Engineering 2022, Vol. 236, issue 16. p. 1–10 https://doi.org/10.1177/09544100221083714
8 Stepan Vasiliv, Nataliya Pryadko, Hennadii Strelnikov and Sergiy Dzuba Application of detonation in impulse systems of energy engineering and mining industry // 2023 IOP Conf. Ser.: Earth Environ. Sci. 1156 012004. p. 1-8.
9 Oleksandr Ihnatiev, Hanna Shevelova1, Hennadii Strelnykov and Borys Blyuss Numerical study of parameters of unit for supplying additional gas flow in jet mill ejector // 2023 IOP Conf. Ser.: Earth Environ. Sci. 1156 012018. p. 1-6.
OFFICE ADDRESS: | Institute of Technical Mechanics , 15 Leshko-Popelya St., Dnipro, Ukraine 49005 |
PHONE NUMBER: | +38-056-372-06-45 |
E-MAIL: | office.itm@nas.gov.ua |