Acting head of department – PhD, senior researcher Tetiana F. Mokriy

Field of research – random oscillations and motion stability of mechanical systems; identification and optimization of their parameters; vibration protection of structures; prediction of vibration load and strength of engineering structures, including vehicles and rocket and space technology products, at operational and excess loads; dynamics of land, air, sea types of launch of liquid-propellant launch vehicles for spacecraft and dynamics of launch of operational tactical missiles and multiple launch rockets; stationary and non-stationary oscillations of an inhomogeneous freight train; dynamic workload and stress-strain state of structural elements of the passenger train crews with a passive safety system under operational driving conditions and emergency collisions, stability and safety of high-speed rolling stock traffic.
A brief history of research in the department. The Department of Statistical Dynamics and Dynamics of Multidimensional Mechanical Systems was formed in 2016 by merging two divisions of the institute (“Department of Statistical Dynamics of Mechanical Systems”, “Department of Dynamics of Multidimensional Mechanical Systems”), which were engaged in researching the dynamics of complex objects, mainly railway rolling stock composition The first head of the united department was the corresponding member of the NASU, Doctor of Technical Sciences, Prof. V. F. Ushkalov. Over the years of the department’s existence, many important theoretical and practical results have been obtained. Effective methods of studying steady and unsteady random oscillations of complex mechanical systems have been developed, methods to identify and optimize their parameters have been proposed; mathematical simulations and methods have been developed to solve the problems of statistical dynamics of vehicles and transported goods. Using these methods, a number of problems of important economic importance have been solved, in particular, problems of vibration protection of machine structures and buildings, including various vehicles, masts, television towers; forecasting the vibration load of rocket and space technology products in land, sea and air transportation. Recommendations have been developed to select the main parameters of designed universal and specialized rail carriages, rational from the point of view of ensuring their strength and dynamic qualities, reliability and vibration protection of transported goods, traffic safety. For example, the specialists of the department participated in the creation of a platform car for the transportation of heavy-duty containers, a long-base universal platform with increased axle load, bunker-type cars for bulk transportation of flour and polymers, multi-axle transporters with a carrying capacity of 700 tons, a car for the transportation of trucks, a rake truck, dump trucks, mixers, specialized undercarriages for freight cars, a unified undercarriage of multiaxle transporters, electric train cars, trolleybuses, trams, a series of special rolling stock for transporting objects of rocket and space technology.
Participation in the creation of objects of new transport engineering technology was recognized with government awards, the Diploma of the State Technical University of the USSR, medals of the VDNG of the USSR and the VDNG of Ukraine.
Mathematical simulations and software for the automated control system of vehicle vibration tests at the bench of the Yuzhnoye State Design Office has been developed.
Specialists of the department have developed methods and software to research the dynamics of land, air and sea launch types of spacecraft launch, taking into account the peculiarities of the non-linear interaction of the spacecraft with the launcher, the variability of the wind flow velocity along the length of the spacecraft, the possibility of asynchronous start-up of the first stage engines and change in the structure of the system in the process of movement. The developed mathematical models and software were used by the the Yuzhnoye State Design Office during the development of the launch technology of the “Zenit”, “Dnipro”, “Cyclone” class launch vehicles and the selection of cyclograms for the launch of engines.
Methods and software have been developed for the study of the dynamic loading of spacecraft launch vehicles and were included as part of a series of works awarded the Prize of the NAS of Ukraine named after M.K. Yangel in 1998.
A mathematical model of the interaction of the launcher support elements with the soil under the action of a short-term dynamic load has been developed to analyze the dynamics of the launch of operational tactical missiles and multiple launch rockets, as well as to assess the residual deformations of the soil base.
Theoretical studies have been performed on the selection of parameters of elastically dissipative devices that provide a significant reduction in vibration loads acting on the spacecraft during air, road and rail transportation.
The department has conducted a study to determine the hydrodynamic characteristics of tanks, partially filled with liquid. A number of practically important experimental results were obtained.
Methods and mathematical simulations have been developed to study the dynamics, loading and stress-deformation state of structural elements of tank cars, including those equipped with means to protect the bottoms from puncture in an emergency situation, during operational and above-standard impact actions.
Technical proposals and practical recommendations on the creation of effective means to protect the bottoms of the boilers of new-generation tank cars in emergency situations have been developed.
The research results were used when creating, together with the Mariupol Heavy Machine Building Plant, a new frameless design of a four-axle tank car for Indian railways and a tank car and a tank car for transportation of liquefied gas.
The main directions of research at present:
- upgrade of domestic rolling stock with the aim to increase the movement velocity of railway crews, improve dynamic qualities, increase the resource of running parts;
- improvement of the “wheel-rail” contact pair, reduction of wear and tear of rolling stock and track elements;
- the development of scientifically based solutions related to ensure the safety of passenger and cargo transportation, as well as the creation of railway crews equipped with passive protection means;
- development of energy absorption devices of the passive safety system of the passenger locomotive, main car and intermediate passenger cars of the high-speed motor train;
- assessment of the operational load of the load-bearing elements of the structures of freight cars with interchangeable bodies and the development of recommendations for fastening elements that ensure the safety of transportation of various loads in wagons with interchangeable bodies;
- study of biomechanics of total hip joint replacement.
The most important achievements of recent years. Mathematical models and appropriate software have been created for the study of spatial oscillations of railway crews taking into account their design features, physical and geometric nonlinearities of the system, the operation of self-coupling devices, the technical condition of the rail track, and the specifics of the transported cargo.
Techniques have been developed that allow using computer simulation to investigate the dynamic processes that occur during the movement of individual wagons and locomotives and trains on sections of track of arbitrary outline both in operational modes and in emergency situations associated with the possibility of individual wagons leaving rails, collision of trains and collision of a train with an obstacle.
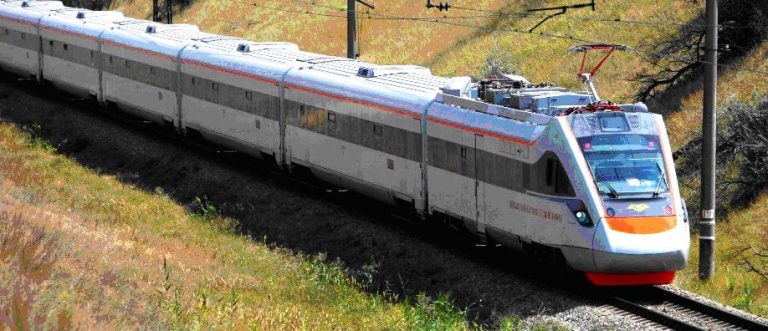
Based on theoretical studies, a system of technical diagnostics of the condition of the running parts of the passenger train has been developed. The system allows to carry out operational control of the technical condition of running parts of cars and track directly in the process of movement, which contributes to increasing the safety of the transportation process.
A methodology based on the synthesis of automated geometric design and finite element modeling has been developed for researching the stress-strain state of structural elements of locomotives and passenger cars equipped with passive protection devices under impact loads typical of operation and emergency collisions.
Mathematical simulations have been developed for the dynamic analysis of elastoplastic deformation of the cabin frame elements of a high-speed passenger locomotive with a passive safety system under shock loads that occur in emergency situations.
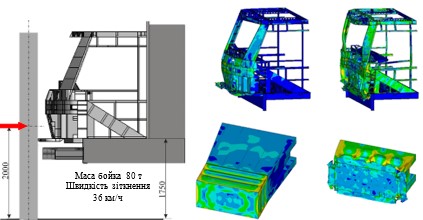
The design of an energy absorption device for the passive safety system of a passenger locomotive in emergency collisions was developed and patented in Ukraine, and its full-scale crash test was performed at the test site in Görlitz (Germany).
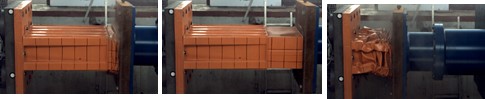
Based on the results of the research, a modular cabin of a new generation high-speed passenger electric locomotive driver with elements of a passive safety system was developed, manufactured and put into production. An electric locomotive with a developed cabin and energy absorption devices was put into operation.
Mathematical models have been developed to study the dynamic loading of the main car of a high-speed motorcar train in emergency collisions, the scenarios of which correspond to the Ukrainian Standard EN 15227 standard on passive safety. The scheme for installing energy absorption devices (EAD) in the end parts of the main and intermediate cars, as well as the design of the EAD for the cars of the motorcar train, has been developed. As a result of mathematical modeling of the dynamics of reference trains in the event of emergency collisions, it has been proven that the proposed devices allow to ensure the protection of passengers and service personnel in emergency collisions in accordance with the requirements of the Ukrainian Standard EN 15227.
Finite-element models have been developed to study the stress-strain state of elements of a freight car with a variable body under normative loads according to the Ukrainian Standard EN 12663-2:2018.
A series of theoretical and experimental studies has been conducted that are closely related to solving the problem of updating the freight fleet of Ukraine’s railways in order to increase the dynamic qualities of crews, increase the resource of running gears, and reduce wear on rolling stock and track elements. Based on the results of these studies, a comprehensive upgrade of freight car trolleys was proposed. In wheelchairs, poorly functioning standard side-bearings with constant-contact side-bearings were replaced; instead of steel wedges, wedges of ductile iron are installed; friction plates are replaced by steel wear-resistant; polymer gaskets are laid in the thrust bearing. At the same time, the best models of the upgrade elements of the company’s development A. Stakey (USA) were used. The wheel rim profile has also been changed to non-linear wear-resistant ITM-73 (the ITM development).
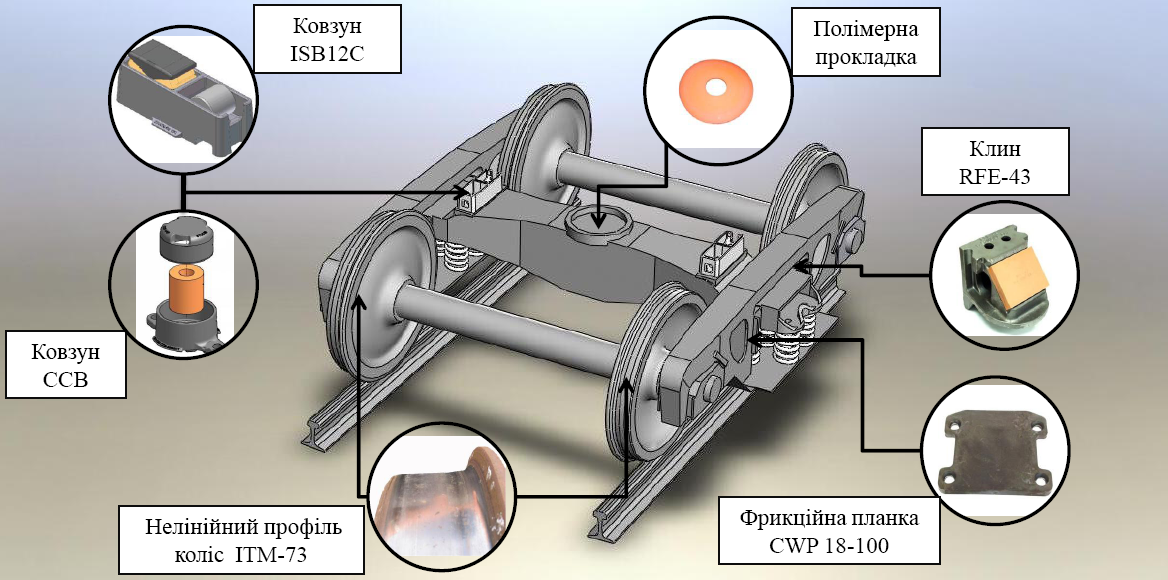
Using this upgrade, it was possible to achieve a more than twofold increase in the wheel resource in terms of flange wear, a more than tenfold decrease in wear in the wedge damping system, a 4-5-fold reduction in the wear of the center plate arrangement.
Since 2004, a comprehensive upgrade of trolleys, mainly gondola cars, the percentage of which in the freight car fleet is about 48%, has been conducated on Ukrainian railways. Now with upgraded carts on the Ukrainian railways, more than 24,000 wagons are operated (about 33% of the gondola car fleet).
Elements of the ITM’s proposed comprehensive upgrade of standard bogies were fully used in the creation of the first three models of Ukrainian freight wagon bogies: models 18-7020 and 18-7033 developed by Kryukovsky Car Building Plant, as well as models 18-4129 developed by KB Sofia-Invest LLC. The first of these bogies was put into mass production, while others have successfully passed experimental tests.
The indicated modernization of the carts was proposed for implementation on the railways of other countries with a gauge of 1520 mm.
To continue the work to improve the comprehensive upgrade of freight car carts, a new, more wear-resistant ITM-73-01 wheel profile was created.
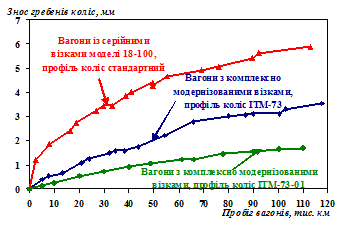
As operational tests of freight cars with comprehensively modernized bogies have shown, the use of the ITM-73 profile first for unworn wheels, and then the ITM-73-01 profile for retreading, allows you to increase the life of the wheels (compared to standard wheels) by more than four times. By the order of Ukrzaliznytsia, the use of the ITM-73-01 profile was made mandatory when regrinding the wheels of comprehensively modernized carts of freight cars.
Work on creating profiles continues. Wear-resistant profiles ITM-73-02 and ITM-73-03 were developed for turning new wheels with a ridge thickness of 32 mm for wagons with new generation trolleys with normal (23.5 ts) and increased to 25 ts axial load on the rails, respectively. The Technical Council of Ukrzaliznytsia made a decision to introduce the ITM-73-02 wheel profile to the design documentation for the new generation model 18-7020 trolley and conduct the corresponding tests of cars with such wheels (however, such tests did not take place due to lack of funding).
A new wear-resistant profile of wheel rims ITM-73EP has been developed for use in sliding wheelsets of passenger cars for the purpose of continuous transfer of trains to the track with other parameters in the conditions of their joint operation on Ukrainian and European railways. Similar studies are being carried out on the creation of a wheel profile for sliding wheel pairs of freight cars, as well as a universal wheel profile for passenger and freight rolling stock.
One of the areas of work of the department is the study of the biomechanics of total hip arthroplasty in cooperation with specialists of the Dnipro State Medical University. To assess the stress-strain state of the bone-implant system during its operation, finite-element calculation models have been developed both for a healthy hip joint and in the case of using an endoprosthesis with various types of acetabular component, which is installed by pressing or screwing into the acetabulum.
![]() | ![]() | ![]() |
Total endoprosthesis for hip joint ORTAN | The computational model of the “bone-acetabular component” system | Intense state of the subchondral bone of the acetabulum under static load |
The main results are published in the books and articles:
- Ushkalov V. F. Statistical dynamics of rail vehicles / V. F. Ushkalov, L. M. Reznikov, S. F. Redko – Kiev : Naukova dumka, 1982. – 360 pp.
- Self-oscillations and Rail Vehicle Motion Stability (in Russian) / Yu.V. Demin, L.A. Dlugach, M.L. Korotenko, O.M. Markova. – Kiev : Naukova Dumka, 1984. – 160 pp.
- Redko S. F. Identification of mechanical systems. Determination of the dynamic characteristics and parameters / S. F. Redko, V. F. Ushkalov, V. P. Yakovlev – Kiev : Naukova dumka, 1985. – 216 pp.
- Demin Yu. V. Dynamics of engineering and transport structures at non-stationary effects / Yu. V. Demin, G. I. Bogomaz, N. Yu. Naumenko. – Kiev : Naukova dumka, 1995. – 189 pp.
- Bogomaz G. I. Liquid fluctuations in tanks / G. I. Bogomaz, S. A. Sirota. – Dnipro : ITM of the NASU and SSAU, 2002. – 305 pp.
- Bogomaz G. I. Dynamics of rail tank cars / G. I. Bogomaz. Kiev : Naukova dumka, 2004. – 223 pp.
- The dynamics of the start in liquid-propellant spacecraft launch vehicles / G. I. Bogomaz, N. Yu. Naumenko, M. B. Sobolevskaya, I. Yu. Hizha. – Kiev : Naukova dumka, 2005. – 248 pp.
- Rail vehicle dynamics and associated problems / A. Sladkowski, H. Scheffel, H. Kovtun, O. Markova, W. Kik, D. Moelle. – Gliwice : Silesian University of Technology, 2005. – 118 p.
- Stress loading of tank cars with transient trains / G. I. Bogomaz, N. Yu. Naumenko, A. N. Pshinko, S. V. Myamlin. – Kiev : Naukova dumka, 2010. – 215 pp.
- Ushkalov V. F. Freight-car truck retrofit as the upgrade option of freight rolling stock running parts / V. F. Ushkalov, A. D. Lashko, T. F. Mokriy // Vestnik of Joint Stock Company Railway Research Institute. – 2013. – # 5. – P. 8 – 15.
- Sobolevska M. Passive safety system of an electric locomotive for high-speed operation on the railways with 1520 mm gauge / M. Sobolevska, I. Telychko (Соболевская М.Б. Система пассивной безопасности пассажирского электровоза для скоростного движения по колее 1520 мм / М. Соболевская, И. Теличко) // Passive Safety of Rail Vehicles 2013 : Railway Research Network Proceedings of the 9th International Symposium “Passive Safety 2013 – Passive Safety of Rail Vehicles and Safe Interiors” in Berlin on 21 – 22 February 2013. – 43/2013. – Berlin : IFV Bahntechnik e.V. – 2013. – P. 63 – 80.
- Naumenko N. Ye., Markova O. M., Kovtun Ye. N., Malyi V. V. Measurement of strains of soil base under short-time loads // Тekhnicheskaya Мekhanika, 2015, # 2 , р. 71-78
- Markova O. Modelling train motion along arbitrary shaped track in transient regimes / O. Markova, H. Kovtun, V. Maliy // Rail and Rapid Transit. – 2015. – Vol. 229(1). – P. 97-105.
- Sobolevska M., Telychko I. Рassive safety of high-speed passenger trains at accident collisions on 1520 mm gauge railways. Transport problems. V. 12. Issue 1. 2017. Р 51 – 62.
- Ushkalov V. F., Mokriy T. F., Malysheva I. Yu., Bezrukavy N. V. Wear-resistant wheel profile for a freight car with increased axial load. Technical mechanics. 2018. No. 1. P. 20 – 29.
- Reduction of freight car wheel wear of 1520 mm gauge railways. / V. Ushkalov, T. Mokriy, I. Malysheva, L. Lapina, S. Pasichnik and N. Bezrukavyi. – IOP Conf. Series: Materials Science and Engineering 985 (2020) 012004 doi:10.1088/1757-899X/985/1/012004.
- Sobolevskaya M., Naumenko N. and Gorobets D. Development of passive protection devices for a power head of a high-speed multiple unit train at its collisions according to DSTU EN 15227. IOP Conf. Series: Materials Science and Engineering 985 (2020) 012016 doi:10.1088/1757-899X/985/1/012016.
- Markova O., Kovtun H. and Maliy V. 3D model to study transitional regimes of train motion. IOP Conf. Series: Materials Science and Engineering 985 (2020) 012003. – doi:10.1088/1757-899X/985/1/012003.
- Sobolevska M. B., Horobets D. V. Recommendations for the manufacture of devices for passive protection of the main car from different materials. Technical mechanics. – 2022. – No. 2. – P. 101 – 114.
- Mokrii T. F., Malysheva I. Yu., Lapina L. G., Bezrukavyi N. V. Rim profile of passenger car wheels for conditions of joint operation on Ukrainian and European railways. Technical mechanics. 2022. No. 4. P. 111 – 120.
On a number of issues related to solving the problems of dynamics of engineering and transport structures, the department cooperates with the PJSC Krukovka Carriage Works, LLC “International Business Cooperation”, Ukrainian State University of Science and Technology, Lviv Research Institute of Forensic Examinations, Dnipro State University of Medical Academy, actively cooperating on improving rolling stock designs with American companies, “A. Staki “and” Amsted Rail “, the German company” EST Eisenbahn-Systemtechnik GmbH “.
OFFICE ADDRESS: | Institute of Technical Mechanics , 15 Leshko-Popelya St., 49005, Dnipro, Ukraine, |
PHONE NUMBER: | +38-056-376-45-94 |
E-MAIL: | victush@gmail.com |