Essence of the technology
Сomputer simulation of fast hydro- and gas-dynamic processes in complex hydraulic systems, which include manifolds, pilot-controlled valves, tanks, throttle valves, dead legs, etc., for the choice and substantiation of the design and operating parameters of specific engineering systems.
Advantages
- Аccounting for: the design features of hydraulic lines (pipe diameters, wall thickness, material); the physical and chemical liquid/gas properties; the hydraulic resistance of feed pipelines and control valves; the degree of gas saturation, gas release and discontinuity of flows; the propagation of wave processes in the system elements; the dynamics of electrically or pneumatically controlled valves; thermogas dynamic processes at the system outlets;
- Unified method for the representation of a branched hydraulic system and its operating conditions.
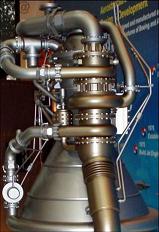
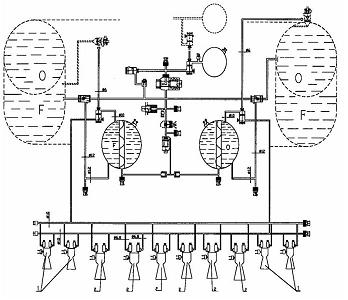
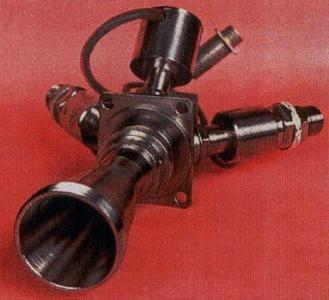
Operational testing
Аs applied to the feed system of two-component liquid-propellant spacecraft flight control thrusters (30 to 100 N thrusters: 8 to 20; simultaneously operating thrusters: 2 to 8). The characteristic times of mode switching (100 to 200 ms), propellant valve response (30 to 40 ms) and wave process propagation (5 to 20 ms) are comparable with one another.
Purpose
The choice, substantiation and optimization of the design parameters of complex branched hydraulic systems of airborne and space vehicles, rocket and internal-combustion engine fuel supply systems, urban water distribution systems, etc. operating in transient conditions (startup and shutdown transients, hydraulic shock, manifold restructuring, gas release, discontinuities).
Time history of the pressure in the combustors of thrusters 1, 2, and 3 when the thrusters are started sequentially
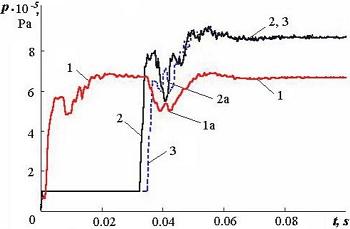
Effect of the propellant ignition delay time τ1 , the electric-valve armature breakaway delay time τ2 , and the valve opening time on the thruster startup
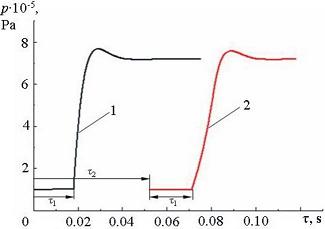
Contact information: | |
Institute of Technical Mechanics of the NASU and SSAU | |
Ukraine 49005 Dnipro 15 Leshko-Popel St. | |
Contact person: | V.I. Tymoshenko |
Phone: | (056) 372 06 41 |
E-mail: | vitymoshenko@nas.gov.ua office.itm@nas.gov.ua |
Web: | http://www.itm.dp.ua |